Sabemos que os produtos manufacturados nunca podem corresponder perfeitamente aos seus desenhos teóricos. O tamanho real varia em função do desenho pretendido. O objectivo de GD&T é manter esta variação dentro dos limites estabelecidos.
P>Posição verdadeira é um GD&T chamada para especificar a posição de uma característica. É mais correctamente referida como “posição”. Usamos este conceito em GD&T para controlar a variação de uma característica específica a partir da sua posição desejada. Isto é importante para o acasalamento de peças para assegurar uma montagem sem costura.
Por exemplo, os furos dos parafusos numa tampa de cabeça de cilindro devem corresponder aos furos dos parafusos na caixa do motor, tanto em tamanho como em posição. Caso contrário, as duas peças não acasalarão, e o óleo lubrificante para a montagem da válvula vazará para fora, derrotando a finalidade da tampa. A tampa do cilindro é inútil, e uma peça diferente deve ser usada.
Para evitar que isto aconteça, usamos tolerâncias de posição como orientação para serviços de torneamento e fresagem CNC.
O símbolo de posição é extremamente útil, mas a sua aplicação pode ser um pouco complicada. Neste artigo, aprenderemos o básico desta chamada de característica e como aplicar esta ferramenta a diferentes condições materiais.
Definição de Posição Verdadeira
A tolerância de posição verdadeira em GD&T informa-nos do desvio máximo permitido de uma característica (por exemplo, furo, ranhura) da sua posição verdadeira. Por posição verdadeira, entendemos a posição ideal da característica de acordo com o desenho.
A ideia é que, para uma característica, existe uma posição verdadeira que desejamos. Definimos planos de referência e eixos como referências para definir a colocação exacta.
Aí, marcamos as posições verdadeiras das características de tamanho utilizando dimensões básicas. Levamos em conta quaisquer modificadores de condição material, se necessário.
Posição é uma tolerância 2D/3D em GD&T que define zonas de tolerância em função da característica. Para características cilíndricas, cria uma zona de tolerância cilíndrica em torno da verdadeira posição da característica dentro da qual o eixo da característica deve situar-se para todos os produtos fabricados.
Para outras características, são definidos planos paralelos dentro dos quais o plano central da característica deve situar-se para aprovação.
Diferença entre Posição e Posição Verdadeira
Na norma ASME Y14.5, a chamada de posição verdadeira é referida como apenas “posição”. “Posição” é a forma correcta de a denominar, pois sabemos que posição verdadeira se refere realmente ao ponto teórico na superfície com dimensões básicas que é impossível de replicar em produtos reais.
No entanto, em CNC machining vernacular, o termo posição verdadeira é mais popular quando se refere à posição da característica no produto real.
Por isso, quando usamos o termo ‘posição verdadeira’ no artigo, na maioria das vezes, referimo-nos à posição da característica fabricada em relação à posição verdadeira real e não à posição verdadeira (dimensão exacta ou valor nominal) da característica.
Obtenha a sua citação de fabrico em segundos
-
Quote em segundos
-
Curto lead times
-
Delivery by Fractory
Get quote
True Position vs Linear Tolerancing
Usar tolerância posicional permite de facto aos designers usar tolerâncias mais soltas. Há muitas vantagens em utilizar tolerâncias mais frouxas e é por isso que se torna imperativo para nós utilizá-las sempre que possível. Vejamos como usar GD&T permite avaliar dois cenários com especificações de tolerância semelhantes.
Posição verdadeira
Considerar um furo definido com uma tolerância posicional de 1 mm. Isto define uma zona de tolerância circular de 0,5 mm de raio em torno da posição real. O eixo do elemento fabricado deve estar dentro deste círculo ⌀1mm, o que significa que a distância máxima do ponto pretendido do eixo é a mesma em todas as direcções.
Agora, considere um ponto dentro desta zona de tolerância a uma distância de 0,25 mm do eixo X e 0,25 mm do eixo Y (considerando a posição verdadeira como origem).
Neste ponto, a posição do elemento é calculada como ~0,7 mm, como posição = 2 x √(x2 + y2). Este número situa-se dentro de 1 mm, e assim, o produto final está dentro da gama aceitável.
Se quisermos que esta posição seja o limite superior, teremos de definir a tolerância posicional como ⌀0.7 mm.
Plus/minus tolerancing
Agora, vamos comparar isto com a tolerância mais/minus.
Plus/minus tolerancing refere-se ao método tradicional de atribuição de tolerâncias a dimensões de características. Devido aos limites superior e inferior atribuídos em cada direcção, a zona de tolerância resultante é um quadrado.
Para aceitar o produto fabricado acima, teríamos de estabelecer um limite de tolerância de ±0,35 mm (Largura de tolerância total = 0,7 mm). Isto definiria um quadrado de lado 0,7 mm.
Ao mesmo tempo, os cantos do quadrado estão mais afastados do que os lados. Isto significa que a tolerância dada usando os eixos X e Y não é uniforme em todas as direcções.
Comparação
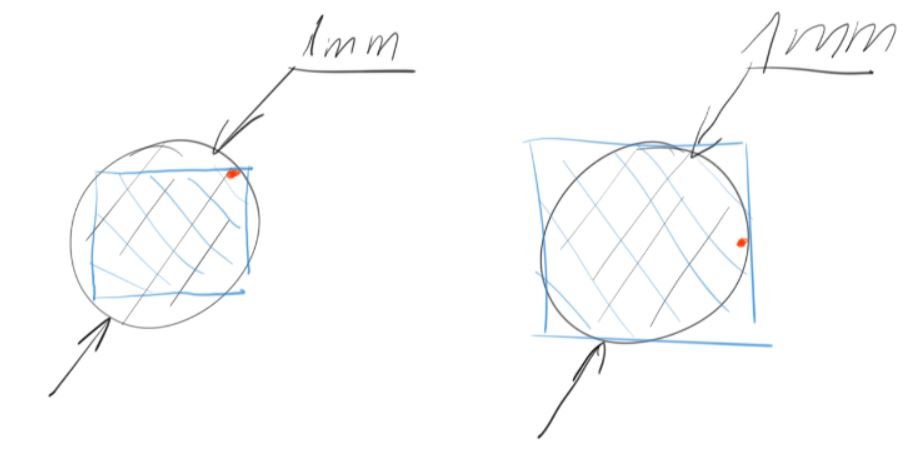
Para que o mesmo ponto se situe em ambas as zonas de tolerância, a zona de tolerância circular irá circunscrever a zona de tolerância quadrada. Se compararmos a área de duas zonas, a área da zona circular excede a zona quadrada.
Podemos calcular a zona extra dividindo a área do círculo circunscrito pela área do quadrado. Em todos os casos, obtemos um aumento de 57% na zona quando preferimos a tolerância posicional em vez da tolerância mais/menos.
Assim, para o mesmo desvio, podemos usar uma tolerância global mais solta e ainda assim aceitar a parte. Isto reduz o custo de fabrico da peça.
Isto pode ser um pouco difícil de compreender. Temos de nos colocar a questão: Porque é que uma peça é aceitável quando o eixo da característica fabricada está a uma distância de 0,7 mm nos cantos de um quadrado mas não é aceitável em todos os 360 graus?
Utilizar a posição verdadeira ajuda-nos a explorar a área extra de 57%, mantendo essencialmente o mesmo limite.
Características da Zona de Tolerância
A zona de tolerância utilizando a posição verdadeira pode aparecer de duas maneiras dependendo da chamada utilizada – cilíndrica e quadrada.
Zona de tolerância cilíndrica
O símbolo da posição verdadeira em GD&T é representado utilizando um símbolo de cristais (⌖). Quando utilizamos a chamada com um símbolo de diâmetro (⌀), obtemos uma zona de tolerância cilíndrica e é assim que se pretende utilizar a maior parte do tempo.
Usualmente, definimos um dado para fixar a verdadeira posição de acordo com o nosso desenho. Por vezes, podemos utilizar múltiplos datums para localizar com precisão a característica. Denota-se este ponto de referência utilizando dimensões básicas.
Esta posição verdadeira actua como nossa referência para medir o desvio das peças efectivamente fabricadas. A posição verdadeira é normalmente definida no centro da característica que está a ser tolerada. Por exemplo, para um furo, a posição verdadeira é definida no eixo do furo. À sua volta, definimos a zona de tolerância do diâmetro 2D ou 3D com base nas características da característica.
Assim, temos um eixo de referência para o furo na posição verdadeira e a zona de tolerância define o limite até ao qual o eixo da característica real da peça se pode desviar.
A zona de tolerância 3D é basicamente um cilindro virtual fixado à volta do eixo do furo no valor de tolerância e percorre toda a espessura da peça.
Zona de tolerância quadrada
Sem utilizar o sinal de diâmetro, a tolerância de posição real refere-se exactamente à mesma zona quadrada como a tolerância linear tradicional faz.
Isto cria uma zona de tolerância mais apertada como explicado anteriormente e por isso raramente é utilizada. Podemos perder mais de 36% da zona de tolerância usando a chamada desta forma.
Como usar a posição verdadeira
A posição verdadeira é uma das chamadas mais usadas em GD&T. Podemos facilmente controlar a localização de diferentes características, utilizando-a. Fornece um método normalizado para expressar a localização, dissipando qualquer confusão.
Para compreender como aplicar a verdadeira posição a uma característica, precisamos de conhecer a moldura de controlo da característica.
Briefly, a moldura de controlo da característica consiste em três blocos principais.
- Símbolo da característica geométrica
- Valor de tolerância e qualquer modificador de condição material
- Planos ou eixos de dados
Suponhamos que precisamos de mostrar, no nosso desenho, a verdadeira posição e tolerância posicional de um orifício deitado no centro de uma peça que mede 100 x 100 x 50 mm(l x b x h). O tamanho do furo é ⌀1 mm com uma tolerância de ±0,005 mm.
Selecção do tipo de característica geométrica
Desde que estamos a denotar a verdadeira posição na moldura de controlo da característica, vamos denotá-la usando o seu símbolo atribuído da mira (⌖) no bloco do símbolo da característica geométrica.
Selecção dos pontos de referência
Comecemos por seleccionar o nosso plano de referência dos pontos de referência. Podemos utilizar um mínimo de um datum. Os dados podem ser pontos, linhas, ou planos.
Neste exemplo de amostra, seleccionaremos três planos de dados. Nomeamo-los por ordem decrescente de importância.
Para o nosso primeiro datum, seleccionaremos o plano inferior da peça de trabalho. Dar-lhe-emos o nome A. Este datum especifica que o eixo central do furo deve ser perpendicular a este plano. Esta é uma forma de controlo de perpendicularidade.
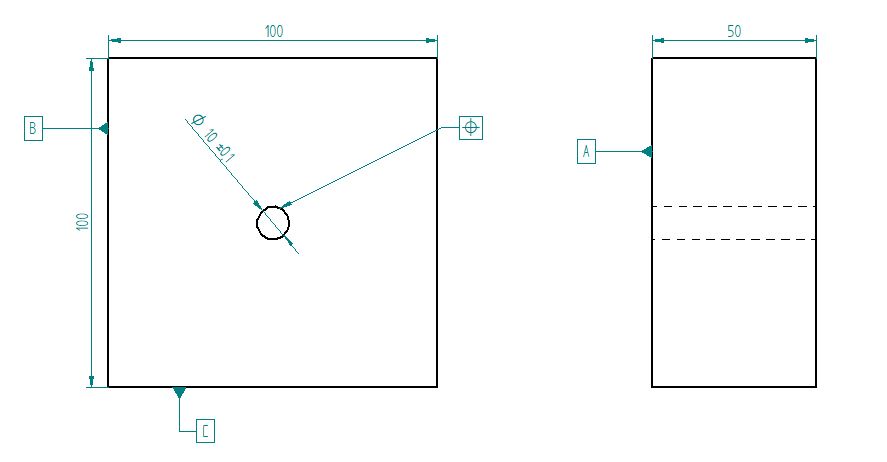
Para o nosso 2º e 3º datum, seleccionaremos os planos da face esquerda e frontal. Marcaremos estes datums como Datum B e C respectivamente no nosso desenho de engenharia.
Então, mencionaremos a distância da nossa característica (furo) dos planos de datum B e C no desenho. Neste caso, é de 50 mm para ambos, pois a posição do furo é no centro. Estas distâncias são mostradas como dimensões básicas e são encerradas numa caixa para exprimir o mesmo.
No quadro de controlo da característica, escreveremos A, B, e C, no 3º, 4º, e 5º blocos respectivamente.
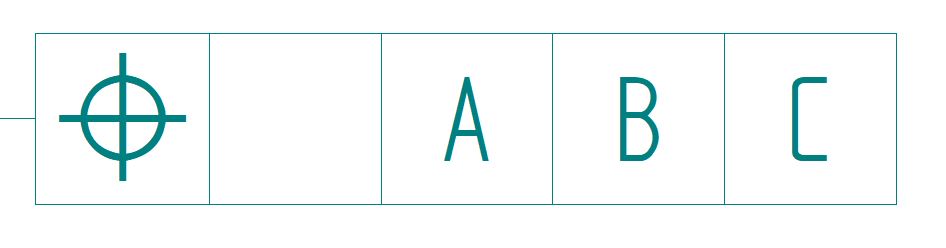
Expressão da zona de tolerância e valores
Neste exemplo, utilizaremos a zona de tolerância cilíndrica. Denotaremos isto na moldura de controlo de características utilizando o símbolo de diâmetro (⌀).
Seguir isto, denota-se a largura de tolerância total como 0,01 mm (±0,005 mm).
Modificadores de condição material
Se existirem quaisquer modificadores de condição material, adicionamo-los após o valor de tolerância. Um ‘M’ circulado para a condição máxima do material (MMC), ou um ‘L’ circulado para a condição mínima do material (LMC). MMC é utilizado mais frequentemente do que LMC.
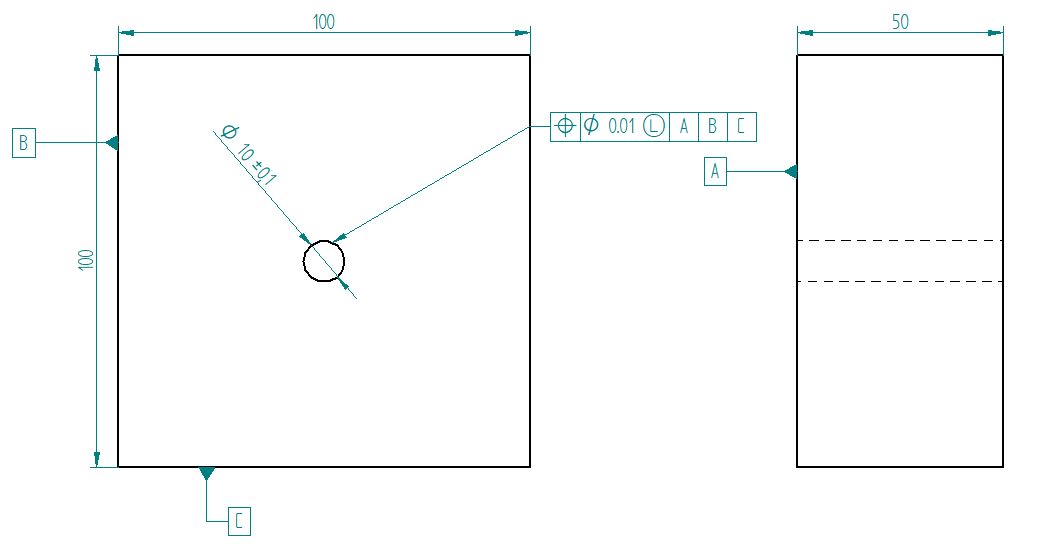
A tolerância de posição real é utilizada muito frequentemente com um modificador da condição do material. As peças são toleradas nestes limites para garantir que não interferem quando acasalam ou se interferem, isso acontece de forma limitada mesmo quando estão nos seus limites de tolerância.
MMC para um eixo é o maior tamanho admissível (diâmetro), e para um furo é o menor tamanho admissível. Podemos assegurar que há sempre alguma folga entre os dois, assegurando que o MMC do veio é inferior ao MMC do furo nos nossos desenhos.
Quando adicionamos este modificador à nossa verdadeira estrutura de controlo de posição, ele especifica que estamos a aplicar as tolerâncias na condição máxima de material para assegurar que um furo não é demasiado pequeno ou um veio demasiado grande em qualquer ponto da profundidade da característica. Assim, com este tamanho de controlo da característica, podemos controlar a orientação para além do tamanho e localização.
Como calcular e medir a verdadeira posição
A verdadeira característica de posição proporciona muitas utilizações. Mas quando se trata de inspecção, é um pouco complicado. Comecemos com como calcular a posição de uma peça fabricada em relação à verdadeira posição da característica.
A verdadeira posição é calculada utilizando a seguinte fórmula:
Posição verdadeira = 2 x Raiz quadrada, onde
Valor medido – Leitura obtida por instrumentos de medição.
Valor verdadeiro – Posição verdadeira declarada usando dimensões básicas.
Estes cálculos podem ser feitos com uma simples calculadora ou manualmente, pois é basicamente o dobro do valor da hipotenusa obtida através do teorema de Pitágoras.
Se o valor obtido estiver dentro do valor da zona definida, aceitamos a peça. Há várias maneiras de realizar as medições da peça. Vejamos estas opções.
Máquina de Medição Coordenada (CMM)
Estas máquinas fornecem alta precisão quando se trata de medições. Normalmente, as lojas de máquinas com máquinas CNC terão uma máquina de medição de coordenadas que mede as peças e faz todos os cálculos digitalmente.
Esta é a forma mais precisa de medir a posição verdadeira. A máquina contém uma bola na extremidade de um braço robótico. Orientamos a bola para a característica que precisamos de medir. Em seguida, traça a característica e converte o movimento no perfil da característica, utilizando o software incorporado.
O método de medição pode ser um pouco confuso. E assim, anotámos os passos gerais que podem ser úteis. Seguimos os seguintes passos ao medir usando uma CMM.
Medir os seus dados
Verificar a impressão e localizar os seus dados. Por exemplo, digamos que A é uma superfície de datum. O datum B é um eixo datum, e C é uma origem datum.
Alinhar a peça
Nivelar o plano. Rodar para a linha e definir a origem como o dado C.
Medir características
Identificar a dimensão chamando a verdadeira posição e medi-la.
Posição da dimensão
Agora, clicar em Dimensão e seleccionar a posição. Em seguida, relate-o.
No caso de estar a utilizar frames de controlo de características, deve definir os dados no editor antes de escolher as características que pretende relatar.
Arter de chamada especial
Podemos utilizar um conjunto especial de paquímetros conhecido como o paquímetro digital de distância central para medir a posição. Esta paquímetro pode medir a distância central entre dois furos ou furos de degrau. Podem medir uma gama de tamanhos centrais de furos.
Podemos usá-la tanto para a medição de passos como para a medição externa. São fáceis de usar com características de bloqueio, ajuste fino, e funções de predefinição de dados.
Medidor funcional fixo
Esta é provavelmente a forma mais rápida de medir a posição real. Vemos geralmente a sua utilização no fabrico de grandes volumes devido à sua eficiência. Um calibre funcional mede apenas a posição e não o tamanho da característica.
Por exemplo, para uma peça com um furo, o calibre seria um bloco com um pino saliente na verdadeira posição do furo e outras características para alinhar com os dados. Se o pino puder entrar no furo quando o calibre estiver alinhado com o datum, aceitamos a peça. O tamanho da característica tem de ser medido separadamente.