Wiemy, że wyprodukowane produkty nigdy nie mogą idealnie pasować do swoich teoretycznych rysunków. Rzeczywisty rozmiar różni się od zamierzonego projektu. Celem GD&T jest utrzymanie tej zmienności w ustalonych granicach.
Pozycja rzeczywista to oznaczenie GD&T służące do określania pozycji elementu. Bardziej poprawnie jest to określane jako „pozycja”. Używamy tej koncepcji w GD&T do kontrolowania odchylenia określonego elementu od jego pożądanej pozycji. Jest to ważne dla współpracujących części, aby zapewnić bezproblemowy montaż.
Na przykład, otwory na śruby w pokrywie głowicy cylindra muszą pasować do otworów na śruby w obudowie silnika zarówno pod względem rozmiaru, jak i pozycji. W przeciwnym razie obie części nie będą do siebie pasować, a olej smarujący zespół zaworów wycieknie, co zniweczy celowość zastosowania pokrywy. Pokrywa cylindra jest bezużyteczna i należy zastosować inny element.
Aby temu zapobiec, stosujemy tolerancje położenia jako wytyczne dla usług toczenia i frezowania CNC.
Symbol położenia jest niezwykle użyteczny, ale jego zastosowanie może być nieco skomplikowane. W tym artykule poznamy podstawy tego symbolu oraz dowiemy się, jak stosować to narzędzie w różnych warunkach materiałowych.
Definicja prawdziwej pozycji
Tolerancja prawdziwej pozycji w GD&T informuje nas o maksymalnym dopuszczalnym odchyleniu elementu (np. otworu, szczeliny) od jego prawdziwej pozycji. Przez prawdziwe położenie rozumiemy idealne położenie elementu zgodnie z projektem.
Pomysł jest taki, że dla elementu istnieje prawdziwe położenie, którego pożądamy. Definiujemy płaszczyzny odniesienia i osie jako punkty odniesienia do określenia dokładnego położenia.
Następnie oznaczamy prawdziwe położenia cech wielkości przy użyciu wymiarów podstawowych. Uwzględniamy wszelkie modyfikatory warunków materiałowych, jeśli są potrzebne.
Pozycja jest tolerancją 2D/3D w GD&T, która definiuje strefy tolerancji w zależności od elementu. Dla elementów cylindrycznych, tworzy ona cylindryczną strefę tolerancji wokół prawdziwej pozycji elementu, w której oś elementu musi leżeć dla wszystkich produkowanych wyrobów.
Dla innych elementów, definiowane są równoległe płaszczyzny, w których płaszczyzna środkowa elementu musi leżeć dla zatwierdzenia.
Różnica pomiędzy pozycją a prawdziwą pozycją
W standardzie ASME Y14.5, wywołanie prawdziwej pozycji jest określane po prostu jako „pozycja”. „Pozycja” jest poprawnym określeniem, ponieważ wiemy, że prawdziwa pozycja odnosi się do teoretycznego punktu na powierzchni o podstawowych wymiarach, który jest niemożliwy do odtworzenia w rzeczywistych produktach.
Jednakże w języku obróbki CNC, termin prawdziwa pozycja jest bardziej popularny w odniesieniu do pozycji elementu na rzeczywistym produkcie.
W związku z tym, kiedy używamy terminu „prawdziwa pozycja” w artykule, częściej niż nie, mamy na myśli pozycję wyprodukowanej cechy w odniesieniu do rzeczywistej prawdziwej pozycji, a nie prawdziwej pozycji (dokładnego wymiaru lub wartości nominalnej) cechy.
Poznaj swoją ofertę produkcyjną w kilka sekund
-
Pytanie w kilka sekund
-
Krótki czas realizacji
-
Dostawa przez Fractory
Get quote
True Position vs Linear Tolerancing
Używanie tolerancji pozycyjnej w rzeczywistości umożliwia projektantom stosowanie luźniejszych tolerancji. Istnieje wiele zalet stosowania luźniejszych tolerancji i dlatego konieczne jest ich stosowanie wszędzie tam, gdzie jest to możliwe. Zobaczmy jak użycie GD&T to umożliwia, oceniając dwa scenariusze z podobnymi specyfikacjami tolerancji.
Prawdziwe położenie
Rozważmy otwór zdefiniowany z tolerancją pozycyjną 1 mm. To definiuje okrągłą strefę tolerancji o promieniu 0.5 mm wokół prawdziwego położenia. Oś produkowanego elementu musi leżeć w tym ⌀1mm okręgu, co oznacza, że maksymalna odległość od zamierzonego miejsca osi jest taka sama w każdym kierunku.
Rozważmy teraz punkt w tej strefie tolerancji w odległości 0,25 mm od osi X i 0,25 mm od osi Y (uznając prawdziwą pozycję za początek).
W tym punkcie pozycja elementu jest obliczana jako ~0,7 mm, jako pozycja = 2 x √(x2 + y2). Ta liczba mieści się w granicach 1 mm, a więc produkt końcowy mieści się w akceptowalnym zakresie.
Jeśli chcemy, aby ta pozycja była górną granicą, będziemy musieli zdefiniować tolerancję pozycji jako ⌀0.7 mm.
Tolerowanie plus/minus
Porównajmy to z tolerowaniem plus/minus.
Tolerowanie plus/minus odnosi się do tradycyjnej metody przypisywania tolerancji do wymiarów elementu. Ze względu na górne i dolne limity przypisane w każdym kierunku, wynikowa strefa tolerancji ma kształt kwadratu.
Aby zaakceptować powyższy produkt, musielibyśmy ustawić limit tolerancji ±0,35 mm (Całkowita szerokość tolerancji = 0,7 mm). Zdefiniowałoby to kwadrat o boku 0,7 mm.
Rogi kwadratu są jednocześnie bardziej oddalone niż boki. Oznacza to, że tolerancja podana przy użyciu osi X i Y nie jest jednakowa w każdym kierunku.
Porównanie
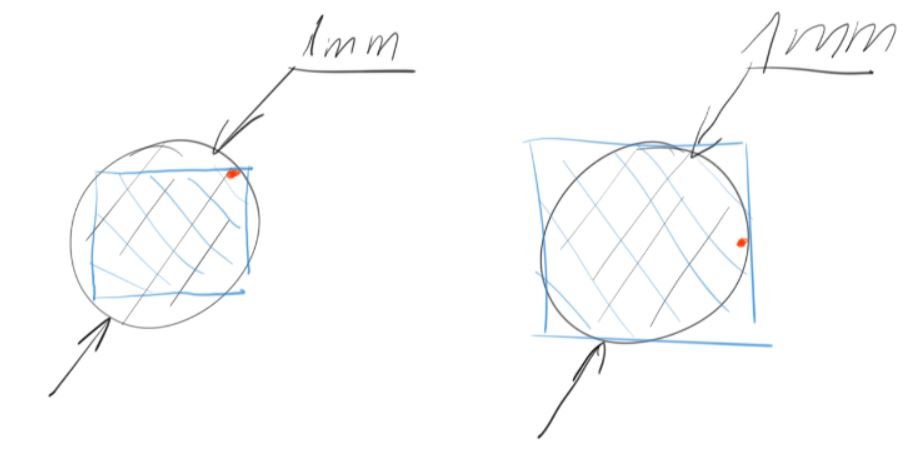
Aby ten sam punkt leżał w obu strefach tolerancji, okrągła strefa tolerancji opasuje kwadratową strefę tolerancji. Jeśli porównamy pola powierzchni dwóch stref, to pole powierzchni strefy kołowej jest większe od pola powierzchni strefy kwadratowej.
Możemy obliczyć dodatkową strefę dzieląc pole powierzchni okręgu przez pole powierzchni kwadratu. We wszystkich przypadkach uzyskujemy 57% wzrost strefy, gdy przedkładamy tolerancję położenia nad tolerancję plus/minus.
W ten sposób, przy tej samej odchyłce, możemy zastosować luźniejszą tolerancję ogólną i nadal zaakceptować część. Obniża to koszt produkcji części.
To może być nieco trudne do zrozumienia. Musimy zadać sobie pytanie: Dlaczego część jest akceptowalna, gdy oś produkowanej cechy znajduje się w odległości 0,7 mm w narożnikach kwadratu, ale nie jest akceptowalna we wszystkich 360 stopniach?
Użycie true position pomaga nam wykorzystać dodatkowe 57% obszaru przy zachowaniu zasadniczo tego samego limitu.
Charakterystyka strefy tolerancji
Strefa tolerancji wykorzystująca true position może pojawić się na dwa sposoby w zależności od użytego wywołania – cylindryczna i kwadratowa.
Cylindryczna strefa tolerancji
Symbol true position w GD&T jest reprezentowany za pomocą symbolu krzyżyka (⌖). Gdy używamy symbolu wywołania z symbolem średnicy (⌀), otrzymujemy cylindryczną strefę tolerancji i tak jest ona przeznaczona do użycia przez większość czasu.
Zazwyczaj ustawiamy punkt odniesienia, aby ustalić prawdziwą pozycję zgodnie z naszym projektem. Czasami, możemy użyć wielu punktów odniesienia, aby dokładnie zlokalizować element. Oznaczamy ten punkt odniesienia za pomocą wymiarów podstawowych.
Ta prawdziwa pozycja działa jako nasze odniesienie do pomiaru odchylenia rzeczywistych produkowanych części. Pozycja rzeczywista jest zwykle ustalana w środku tolerowanego elementu. Na przykład, dla otworu, prawdziwa pozycja jest ustawiona na osi otworu. Wokół niej definiujemy strefę tolerancji średnicy 2D lub 3D w oparciu o charakterystykę elementu.
Więc, mamy oś odniesienia dla otworu w prawdziwej pozycji, a strefa tolerancji określa limit, do którego oś rzeczywistego elementu może się zbaczać.
Strefa tolerancji 3D jest w zasadzie wirtualnym cylindrem ustalonym wokół osi otworu na wartości tolerancji i przechodzi przez całą grubość części.
Kwadratowa strefa tolerancji
Bez użycia znaku średnicy, prawdziwa tolerancja położenia odnosi się do dokładnie takiej samej kwadratowej strefy, jak w przypadku tradycyjnej tolerancji liniowej.
Tworzy to ciaśniejszą strefę tolerancji, jak wyjaśniono wcześniej i dlatego jest rzadko używana. Możemy stracić więcej niż 36% strefy tolerancji używając tego wywołania w ten sposób.
Jak używać True Position
True position jest jednym z najbardziej szeroko używanych wywołań w GD&T. Za jego pomocą możemy w prosty sposób kontrolować położenie różnych elementów. Zapewnia ona znormalizowaną metodę wyrażania położenia, rozwiewając wszelkie niejasności.
Aby zrozumieć, jak zastosować prawdziwe położenie do elementu, potrzebujemy wiedzy na temat ramki kontrolnej elementu.
W skrócie, ramka kontrolna elementu składa się z trzech głównych bloków.
- Symbol charakterystyki geometrycznej
- Wartość tolerancji i dowolny modyfikator stanu materiału
- Płaszczyzny lub osie danych
Załóżmy, że musimy wyświetlić na naszym rysunku prawdziwe położenie i tolerancję położenia otworu leżącego w środku przedmiotu o wymiarach 100 x 100 x 50 mm (l x b x h). Rozmiar otworu wynosi ⌀1 mm z tolerancją ±0,005 mm.
Wybór typu cechy geometrycznej
Ponieważ oznaczamy położenie rzeczywiste w ramce kontrolnej cechy, będziemy je oznaczać za pomocą przypisanego mu symbolu krzyżyka (⌖) w bloku symboli cech geometrycznych.
Wybór punktów odniesienia
Zaczynamy od wyboru naszej płaszczyzny odniesienia. Możemy użyć co najmniej jednego układu odniesienia. Punktami odniesienia mogą być punkty, proste lub płaszczyzny.
W tym przykładowym przykładzie wybierzemy trzy płaszczyzny odniesienia. Nazwiemy je w kolejności malejącej ważności.
Do naszego pierwszego układu odniesienia wybierzemy dolną płaszczyznę przedmiotu. Nazwiemy ją A. Ten układ odniesienia określa, że oś środka otworu musi być prostopadła do tej płaszczyzny. Jest to forma kontroli prostopadłości.
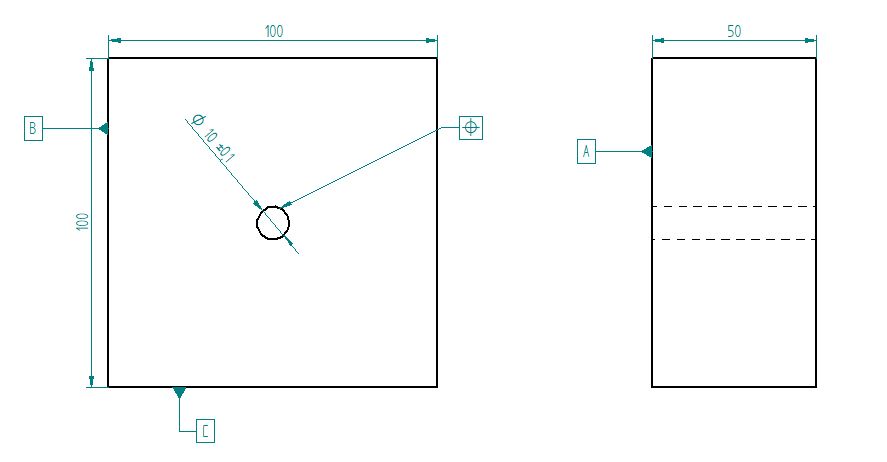
Dla naszego drugiego i trzeciego układu odniesienia, wybierzemy płaszczyzny lewej i przedniej powierzchni. Oznaczymy te punkty odniesienia jako Datum B i C odpowiednio na naszym rysunku inżynierskim.
Następnie podamy odległość naszego elementu (otworu) od płaszczyzn odniesienia B i C na rysunku. W tym przypadku jest to 50 mm dla obu, ponieważ otwór znajduje się w środku. Odległości te są przedstawiane jako wymiary podstawowe i są ujęte w ramkę, aby wyrazić to samo.
W ramce kontrolnej elementu wpiszemy A, B i C, odpowiednio w 3, 4 i 5 bloku.
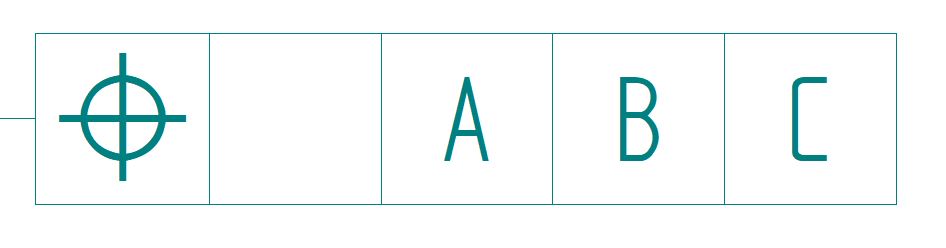
Wyrażanie strefy tolerancji i wartości
W tym przykładzie użyjemy cylindrycznej strefy tolerancji. Oznaczymy ją w ramce kontrolnej elementu za pomocą symbolu średnicy (⌀).
Następnie oznaczymy całkowitą szerokość tolerancji jako 0,01 mm (±0,005 mm).
Modyfikatory warunków materiałowych
Jeśli występują modyfikatory warunków materiałowych, dodajemy je po wartości tolerancji. Przekreślone „M” oznacza maksymalny stan materiału (MMC), lub przekreślone „L” oznacza najmniejszy stan materiału (LMC). MMC jest stosowane częściej niż LMC.
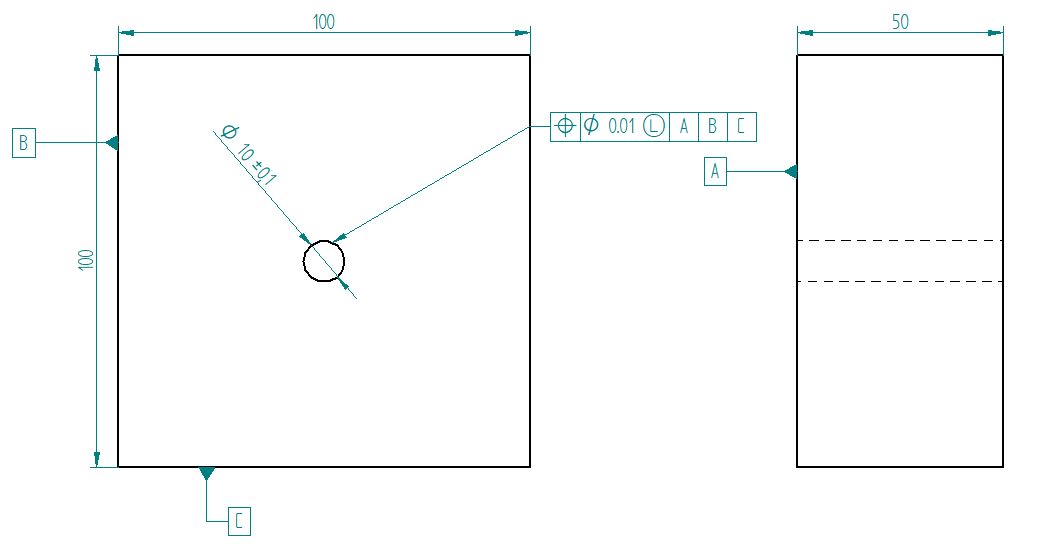
Tolerancja prawdziwego położenia jest stosowana bardzo często z modyfikatorem stanu materiału. Części są tolerowane w tych granicach, aby zapewnić, że nie kolidują ze sobą podczas łączenia lub jeśli tak się dzieje, dzieje się to w ograniczony sposób, nawet jeśli są w swoich granicach tolerancji.
MMC dla wałka jest największym dopuszczalnym rozmiarem (średnicą), a dla otworu najmniejszym dopuszczalnym rozmiarem. Możemy zapewnić, że zawsze istnieje pewien luz pomiędzy tymi dwoma elementami poprzez zapewnienie, że MMC wałka jest mniejsza niż MMC otworu w naszych projektach.
Gdy dodajemy ten modyfikator do naszej rzeczywistej ramy kontroli położenia, określa on, że stosujemy tolerancje przy maksymalnym stanie materiału, aby zapewnić, że otwór nie jest zbyt mały lub wałek zbyt duży w dowolnym punkcie na całej głębokości elementu. W ten sposób, z tym rozmiarem kontroli elementu, możemy kontrolować orientację oprócz rozmiaru i lokalizacji.
Jak obliczyć i zmierzyć pozycję rzeczywistą
Cecha pozycji rzeczywistej ma wiele zastosowań. Ale jeśli chodzi o kontrolę, jest to trochę skomplikowane. Zacznijmy od tego, jak obliczyć pozycję produkowanej części w odniesieniu do prawdziwej pozycji elementu.
Prawdziwa pozycja jest obliczana przy użyciu następującego wzoru:
Prawdziwa pozycja = 2 x pierwiastek kwadratowy, gdzie
Wartość mierzona – Odczyt uzyskany przez przyrządy pomiarowe.
Wartość rzeczywista – Pozycja rzeczywista podana przy użyciu wymiarów podstawowych.
Obliczeń tych można dokonać za pomocą prostego kalkulatora lub ręcznie, gdyż jest to w zasadzie dwukrotność wartości hipotensji uzyskanej za pomocą twierdzenia Pitagorasa.
Jeśli uzyskana wartość mieści się w wartości zdefiniowanej strefy, akceptujemy część. Istnieje kilka sposobów na przeprowadzenie pomiarów części. Przyjrzyjmy się tym opcjom.
Współrzędnościowa maszyna pomiarowa (CMM)
Maszyny te zapewniają wysoką dokładność, jeśli chodzi o pomiary. Zazwyczaj warsztaty maszynowe z maszynami CNC będą miały współrzędnościową maszynę pomiarową, która mierzy części i wykonuje wszystkie obliczenia cyfrowo.
Jest to najdokładniejszy sposób pomiaru prawdziwej pozycji. Maszyna zawiera kulę na końcu zrobotyzowanego ramienia. Naprowadzamy kulę na element, który chcemy zmierzyć. Następnie śledzi ona ten element i przekształca ruch w profil elementu za pomocą wbudowanego oprogramowania.
Metoda pomiaru może być nieco myląca. Dlatego też, zanotowaliśmy ogólne kroki, które mogą okazać się pomocne. Wykonujemy następujące kroki podczas pomiarów przy użyciu maszyny CMM.
Pomiar punktów odniesienia
Sprawdź wydruk i zlokalizuj swoje punkty odniesienia. Na przykład, powiedzmy, że A jest powierzchnią bazową. Punkt B jest osią punktu odniesienia, a C jest początkiem punktu odniesienia.
Wyrównaj część
Poziomuj płaszczyznę. Obróć do linii i ustaw początek jako punkt odniesienia C.
Pomiar cech
Zidentyfikuj wymiar wywołujący prawdziwe położenie i zmierz go.
Pozycja wymiaru
Teraz kliknij na Wymiar i wybierz położenie. Następnie zgłoś ją.
W przypadku, gdy używasz ramek kontrolnych elementów, musisz zdefiniować punkty odniesienia w edytorze przed wybraniem elementów, które chcesz zgłosić.
Specjalna suwmiarka
Do pomiaru pozycji możemy użyć specjalnego zestawu suwmiarek znanego jako suwmiarka cyfrowa odległości środkowej. Suwmiarka ta może mierzyć odległość środka pomiędzy dwoma otworami lub otworami stopniowymi. Może mierzyć różne wielkości środków otworów.
Możemy jej używać do pomiarów stopniowych oraz zewnętrznych. Są one łatwe w użyciu dzięki funkcjom blokowania, dokładnej regulacji i wstępnego ustawiania danych.
Stały przymiar funkcjonalny
Jest to prawdopodobnie najszybszy sposób pomiaru prawdziwej pozycji. Ze względu na swoją wydajność jest on stosowany w produkcji wielkoseryjnej. Przymiar funkcjonalny mierzy tylko pozycję, a nie rozmiar elementu.
Na przykład, dla elementu z otworem, przymiar będzie bloczkiem z wystającym trzpieniem w prawdziwej pozycji otworu i innymi elementami do wyrównania z punktami odniesienia. Jeśli sworzeń może wejść do otworu, gdy sprawdzian jest w linii z układem odniesienia, akceptujemy część. Wielkość elementu musi być mierzona oddzielnie.