We weten dat vervaardigde producten nooit perfect overeen kunnen komen met hun theoretische tekeningen. De werkelijke afmetingen wijken af van het beoogde ontwerp. Het doel van GD&T is om deze variatie binnen bepaalde grenzen te houden.
True position is een GD&T callout voor het specificeren van de positie van een element. Het wordt correcter aangeduid als “positie”. We gebruiken dit concept in GD&T om de variatie van een specifiek element van zijn gewenste positie te controleren. Dit is belangrijk bij het koppelen van onderdelen om een naadloze assemblage te verzekeren.
Bijv. de schroefgaten op een cilinderkopdeksel moeten overeenkomen met de schroefgaten op de motorbehuizing, zowel in grootte als in positie. Als dat niet het geval is, passen de twee delen niet op elkaar en lekt de smeerolie voor de kleppen, waardoor het doel van het deksel teniet wordt gedaan. Het cilinderdeksel is nutteloos, en er moet een ander stuk worden gebruikt.
Om dit te voorkomen, gebruiken we positietoleranties als leidraad voor CNC draai- en freeswerk.
Het positiesymbool is een uiterst nuttig symbool, maar de toepassing ervan kan wat ingewikkeld zijn. In dit artikel zullen we de basis van deze feature callout leren en hoe we dit gereedschap kunnen toepassen op verschillende materiaalcondities.
Definitie van ware positie
De ware positietolerantie in GD&T informeert ons over de maximaal toegestane afwijking van een feature (bijv. gat, sleuf) ten opzichte van zijn ware positie. Met ware positie bedoelen we de ideale positie van de vorm volgens het ontwerp.
Het idee is dat er voor een vorm een ware positie is die we wensen. We definiëren nulpuntvlakken en assen als referenties om de exacte plaatsing te bepalen.
Daarna markeren we de ware posities van de kenmerken van grootte met behulp van basisafmetingen.
Positie is een 2D/3D tolerantie in GD&T die tolerantiezones definieert, afhankelijk van het element. Voor cilindrische elementen wordt een cilindrische tolerantiezone rond de ware positie van het element gecreëerd waarbinnen de as van het element moet liggen voor alle geproduceerde producten.
Voor andere elementen worden parallelle vlakken gedefinieerd waarbinnen het middenvlak van het element moet liggen voor goedkeuring.
Verschil tussen positie en ware positie
In de ASME Y14.5-norm wordt de ware positie callout gewoon “positie” genoemd. “Positie” is de juiste manier om het te noemen, omdat we weten dat de ware positie eigenlijk verwijst naar het theoretische punt op het oppervlak met basisafmetingen die onmogelijk te repliceren zijn in werkelijke producten.
In de volkstaal van CNC-bewerking is de term ware positie echter populairder wanneer het gaat om de positie van het element op het werkelijke product.
Daarom bedoelen we, wanneer we in dit artikel de term ‘ware positie’ gebruiken, meestal de positie van de gefabriceerde vorm ten opzichte van de werkelijke werkelijke positie en niet de werkelijke positie (exacte afmeting of nominale waarde) van de vorm.
Geef uw productie-offerte in enkele seconden
-
Offerte in enkele seconden
-
Korte doorlooptijden
-
Levering door Fractory
Vraag offerte aan
True Position vs Linear Tolerancing
Het gebruik van positietolerantie stelt ontwerpers in feite in staat om lossere toleranties te gebruiken. Er zijn veel voordelen aan het gebruik van ruimere toleranties en daarom is het noodzakelijk dat we ze waar mogelijk gebruiken. Laten we eens kijken hoe het gebruik van GD&T dit mogelijk maakt door twee scenario’s met vergelijkbare toleranties te evalueren.
Trouwe positie
Zie een gat gedefinieerd met een positionele tolerantie van 1 mm. Dit definieert een cirkelvormige tolerantiezone met een straal van 0,5 mm rond de ware positie. De as van de gefabriceerde feature moet binnen deze ⌀1mm cirkel liggen, wat betekent dat de maximale afstand tot de beoogde asplek in elke richting gelijk is.
Nu, beschouw een punt binnen deze tolerantiezone op een afstand van 0,25 mm van de X-as en 0,25 mm van de Y-as (met de ware positie als oorsprong).
Op dit punt wordt de positie van de feature berekend als ~0,7 mm, als positie = 2 x √(x2 + y2). Dit getal ligt binnen 1 mm, en dus ligt het eindproduct binnen het acceptabele bereik.
Als we willen dat deze positie de bovengrens is, moeten we de positietolerantie definiëren als ⌀0,7 mm.
Plus/minus tolerancing
Nu gaan we dit vergelijken met plus/minus tolerancing.
Plus/minus tolerancing verwijst naar de traditionele methode om toleranties toe te kennen aan feature afmetingen. Door de boven- en ondergrenzen die in elke richting worden toegewezen, is de resulterende tolerantiezone een vierkant.
Om het bovenstaande product te accepteren, zouden we een tolerantiegrens van ±0,35 mm moeten instellen (Totale tolerantiebreedte = 0,7 mm). Dit zou een vierkant definiëren met zijde 0,7 mm.
Zelfs zijn de hoeken van het vierkant verder weg dan de zijden. Dit betekent dat de tolerantie die met de X- en Y-as wordt gegeven, niet in alle richtingen gelijk is.
Vergelijking
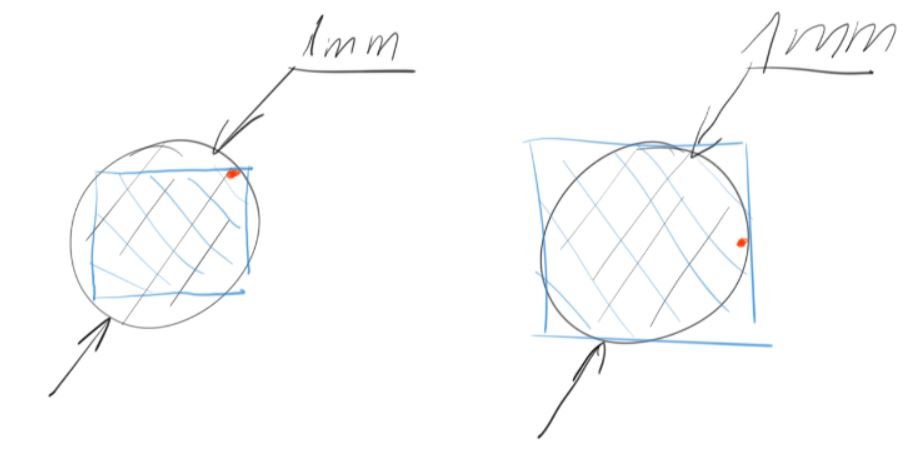
Als hetzelfde punt in beide tolerantiezones ligt, zal de cirkelvormige tolerantiezone de vierkante tolerantiezone omcirkelen. Als we de oppervlakte van de twee zones vergelijken, is de oppervlakte van de cirkelvormige zone groter dan die van de vierkante zone.
We kunnen de extra zone berekenen door de oppervlakte van de omgeschreven cirkel te delen door de oppervlakte van het vierkant. In alle gevallen krijgen we een toename van 57% in de zone wanneer we de voorkeur geven aan de positietolerantie boven de plus/min-tolerantie.
Dus voor dezelfde afwijking kunnen we een ruimere globale tolerantie gebruiken en het onderdeel toch accepteren. Dit verlaagt de fabricagekosten van het onderdeel.
Dit kan een beetje moeilijk te begrijpen zijn. We moeten onszelf de vraag stellen: Waarom is een onderdeel aanvaardbaar wanneer de as van de gefabriceerde vorm zich op een afstand van 0,7 mm op de hoeken van een vierkant bevindt, maar niet aanvaardbaar in alle 360 graden?
Het gebruik van de ware positie helpt ons de extra 57% oppervlakte te benutten, terwijl in wezen dezelfde limiet wordt gehandhaafd.
Karakteristieken van de tolerantiezone
De tolerantiezone bij gebruik van de ware positie kan op twee manieren worden weergegeven, afhankelijk van de gebruikte callout – cilindrisch en vierkant.
Cylindrische tolerantiezone
Het symbool voor de ware positie in GD&T wordt weergegeven met een dradenkruis-symbool (⌖). Als we de callout met een diametersymbool (⌀) gebruiken, krijgen we een cilindrische tolerantiezone en zo is het meestal ook bedoeld.
Normaal gesproken stellen we een nulpunt in om de ware positie vast te leggen volgens ons ontwerp. Soms gebruiken we meerdere referentiepunten om het element nauwkeurig te lokaliseren. We duiden dit referentiepunt aan met behulp van basisafmetingen.
Deze werkelijke positie dient als onze referentie om de afwijking van de werkelijk vervaardigde onderdelen te meten. De ware positie wordt meestal bepaald in het midden van het te tolereren product. Voor een gat bijvoorbeeld, wordt de ware positie bepaald op de as van het gat. Daaromheen definiëren we de tolerantiezone voor de 2D- of 3D-diameter op basis van de kenmerken van het element.
Dus we hebben een referentie-as voor het gat op de ware positie en de tolerantiezone stelt de grens vast tot waar de as van het werkelijke onderdeel mag afwijken.
De 3D-tolerantiezone is in feite een virtuele cilinder die rond de as van het gat op de tolerantiewaarde is bevestigd en door de volledige dikte van het onderdeel loopt.
Vierkante tolerantiezone
Zonder het gebruik van het diameterteken verwijst de ware positietolerantie naar precies dezelfde vierkante zone als de traditionele lineaire tolerantie doet.
Dit creëert een strakkere tolerantiezone zoals eerder uitgelegd en wordt daarom zelden gebruikt. We kunnen meer dan 36% van de tolerantiezone verliezen door de callout op deze manier te gebruiken.
Hoe ware positie te gebruiken
True positie is een van de meest gebruikte callouts in GD&T. We kunnen er gemakkelijk de plaats van verschillende features mee bepalen. Het biedt een gestandaardiseerde methode om de locatie uit te drukken, waardoor elke verwarring wordt weggenomen.
Om te begrijpen hoe we de ware positie kunnen toepassen op een feature, hebben we kennis nodig van het feature control frame.
In het kort, het feature control frame bestaat uit drie hoofdblokken.
- Geometrisch symbool
- Tolerantiewaarde en eventuele materiaaleigenschappen
- Datumvlakken of assen
Stel dat we op onze tekening de ware positie en positietolerantie moeten weergeven van een gat dat in het midden van een werkstuk ligt en 100 x 100 x 50 mm (l x b x h) meet. De afmeting van het gat is ⌀1 mm met een tolerantie van ±0,005 mm.
Selecteren van het type geometrisch kenmerk
Omdat we de ware positie in het feature control frame aangeven, zullen we dit doen met het toegewezen symbool van het dradenkruis (⌖) in het geometrisch karakteristiek symboolblok.
Selecteren van nulpunten
We beginnen met het selecteren van ons referentie-nulpvlak. We kunnen minimaal één referentiepunt gebruiken. Referentiepunten kunnen punten, lijnen of vlakken zijn.
In dit voorbeeld kiezen we drie referentievlakken. We noemen ze in afnemende volgorde van belangrijkheid.
Voor ons eerste referentiepunt kiezen we het onderste vlak van het werkstuk. We noemen het A. Dit nulpunt geeft aan dat de middenas van het gat loodrecht op dit vlak moet staan. Dit is een vorm van loodrechtheidscontrole.
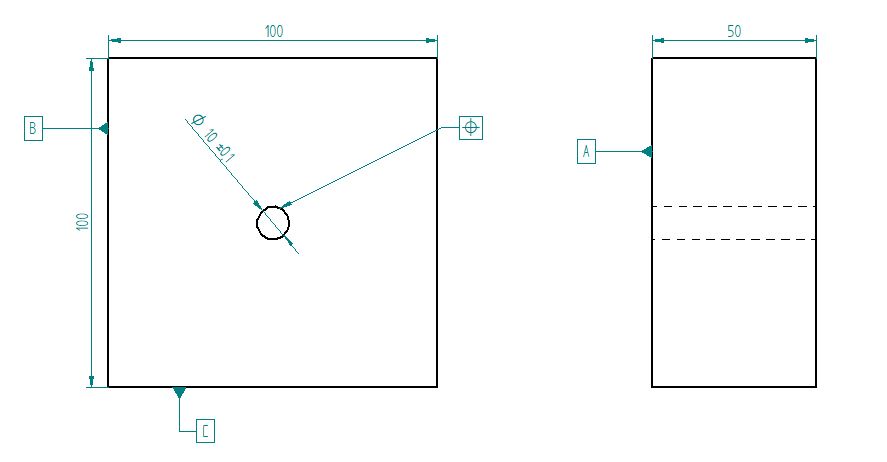
Voor ons 2e en 3e nulpunt kiezen we de vlakken van het linker- en voorvlak. We markeren deze nulpunten als respectievelijk nulpunt B en C op onze technische tekening.
Daarna vermelden we de afstand van onze feature (gat) tot de nulpuntvlakken B en C op de tekening. In dit geval is dat voor beide 50 mm, omdat het gat zich in het midden bevindt. Deze afstanden worden weergegeven als basisafmetingen en zijn ingesloten in een kader om hetzelfde uit te drukken.
In het feature control frame, noteren we A, B, en C, in respectievelijk het 3e, 4e, en 5e blok.
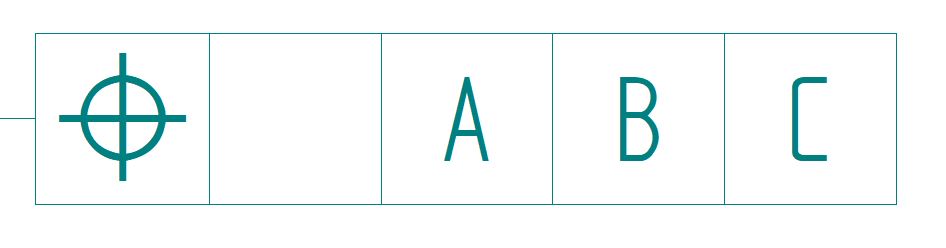
Uitdrukking van de tolerantiezone en waarden
In dit voorbeeld zullen we de cilindrische tolerantiezone gebruiken. Deze geven we in het feature control frame aan met het diametersymbool (⌀).
Daarna geven we de totale tolerantiebreedte aan als 0,01 mm (±0,005 mm).
Materiaalconditie modifiers
Als er materiaalconditie modifiers aanwezig zijn, voegen we die toe na de tolerantiewaarde. Een omcirkelde ‘M’ voor maximale materiaalconditie (MMC), of een omcirkelde ‘L’ voor minste materiaalconditie (LMC). MMC wordt vaker gebruikt dan LMC.
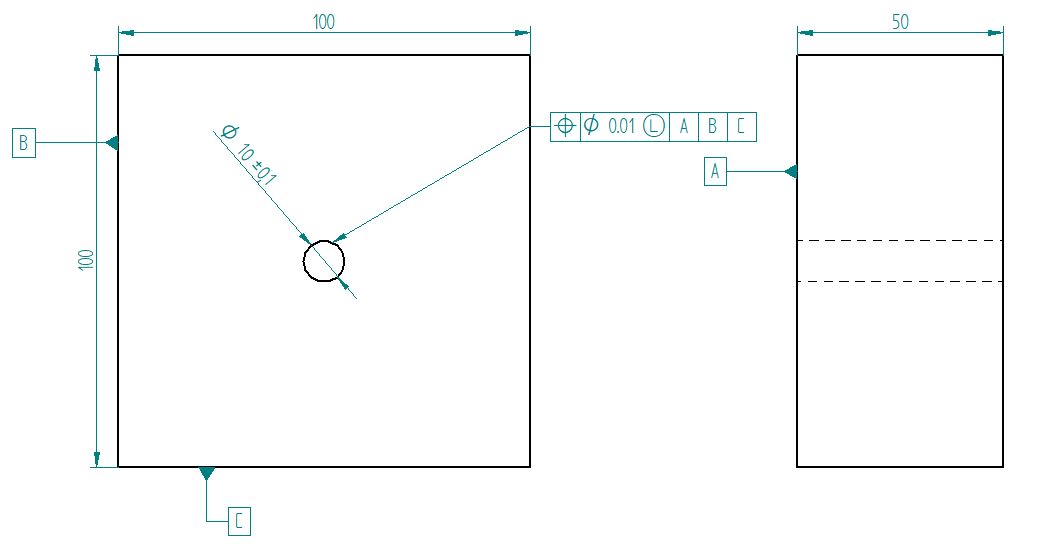
De tolerantie voor de werkelijke positie wordt heel vaak gebruikt met een materiaalconditie modifier. Onderdelen worden op deze grenzen getolereerd om ervoor te zorgen dat ze bij het paren niet met elkaar in conflict komen, of als dat wel gebeurt, gebeurt dat op een beperkte manier, zelfs als ze op hun tolerantiegrens zitten.
MMC voor een as is de grootst toelaatbare maat (diameter), en voor een gat de kleinst toelaatbare maat. We kunnen ervoor zorgen dat er altijd enige speling is tussen de twee door ervoor te zorgen dat de MMC van de as kleiner is dan de MMC van het gat in onze ontwerpen.
Wanneer we deze modifier toevoegen aan ons true position control frame, geeft het aan dat we de toleranties toepassen op de maximale materiaalconditie om ervoor te zorgen dat een gat niet te klein of een as niet te groot is op enig punt over de diepte van de feature. Dus, met deze grootte van feature controle, kunnen we naast de grootte en plaats ook de oriëntatie controleren.
Hoe de ware positie te berekenen en te meten
De ware positie feature biedt vele toepassingen. Maar als het op inspectie aankomt, is het een beetje ingewikkeld. Laten we beginnen met hoe de positie van een gefabriceerd onderdeel te berekenen ten opzichte van de ware positie van het element.
De ware positie wordt berekend met behulp van de volgende formule:
True Position = 2 x Vierkantswortel, waarbij
Gemeten waarde – Aflezing verkregen door meetinstrumenten.
True value – Ware positie opgegeven met behulp van basisafmetingen.
Deze berekeningen kunnen worden uitgevoerd met een eenvoudige rekenmachine of handmatig, aangezien het in principe gaat om het dubbele van de waarde van de hypotenusa verkregen via de stelling van Pythagoras.
Als de verkregen waarde binnen de waarde van de gedefinieerde zone ligt, accepteren we het onderdeel. Er zijn verschillende manieren om de deelmetingen uit te voeren. Laten we deze opties eens bekijken.
Coordinaatmeetmachine (CMM)
Deze machines bieden een hoge nauwkeurigheid als het gaat om metingen. Meestal hebben machinewerkplaatsen met CNC-machines een coördinatenmeetmachine die de onderdelen opmeet en alle berekeningen digitaal uitvoert.
Dit is de meest nauwkeurige manier om de werkelijke positie te meten. De machine bevat een kogel aan het eind van een robotarm. Wij leiden de kogel naar het te meten deel. Vervolgens traceert hij het object en zet de beweging om in het profiel van het object met behulp van de ingebouwde software.
De meetmethode kan een beetje verwarrend zijn. Daarom hebben wij de algemene stappen op een rijtje gezet die van pas kunnen komen. Wij volgen de volgende stappen bij het meten met een CMM.
Met uw nulpunten
Controleer de afdruk en lokaliseer uw nulpunten. Stel bijvoorbeeld dat A een nulpuntoppervlak is. Referentiepunt B is een referentie-as, en C is een referentie-oorsprong.
Lijn het onderdeel uit
Lijn het vlak. Roteer naar de lijn en stel de oorsprong in als referentiepunt C.
Geometrie
Identificeer de dimensie die de ware positie oproept en meet deze.
Dimensioneer positie
Klik nu op Dimensie en selecteer de positie.
In het geval dat u feature control frames gebruikt, moet u de nulpunten in de editor definiëren voordat u de features kiest die u wilt rapporteren.
Speciale schuifmaat
We kunnen een speciale set schuifmaten gebruiken die bekend staat als de digitale schuifmaat met middenafstand om de positie te meten. Deze krompasser kan de centrumafstand tussen twee gaten of stapgaten meten. Zij kunnen een waaier van de grootte van het gatencentrum meten.
Wij kunnen het voor stap zowel als externe meting gebruiken. Ze zijn gemakkelijk te gebruiken met vergrendelingsfuncties, fijnafstelling en functies voor het vooraf instellen van gegevens.
Vaste functionele schuifmaat
Dit is waarschijnlijk de snelste manier om de ware positie te meten. Vanwege de efficiëntie wordt deze methode meestal gebruikt in de massaproductie.
Voor een werkstuk met een gat bijvoorbeeld, zou de meter een blok zijn met een uitstekende pin op de ware positie van het gat en andere elementen om uit te lijnen op de referentiepunten. Als de pen het gat kan binnengaan wanneer de meter in lijn is met het nulpunt, accepteren we het werkstuk. De afmetingen van de elementen moeten apart worden gemeten.