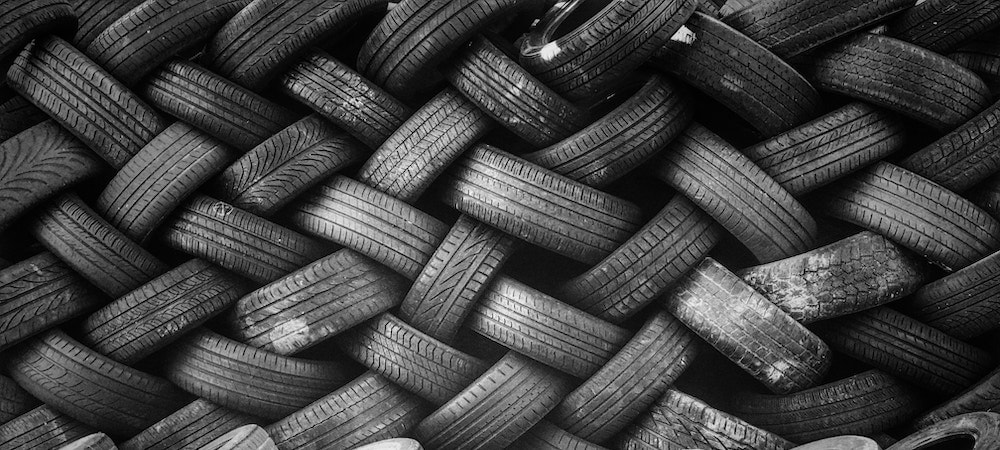

FMEA – failure mode and effects analysis – is een hulpmiddel voor het identificeren van potentiële problemen en hun impact.
Problemen en defecten zijn duur. Het is begrijpelijk dat klanten hoge verwachtingen stellen aan fabrikanten en dienstverleners om kwaliteit en betrouwbaarheid te leveren.
Vaak worden fouten in producten en diensten ontdekt door uitgebreide tests en voorspellende modellering in latere stadia van ontwikkeling. Het vinden van een probleem op dit punt in de cyclus kan echter aanzienlijke kosten en vertragingen in de planning met zich meebrengen. De uitdaging is om kwaliteit en betrouwbaarheid aan het begin van het proces te ontwerpen en ervoor te zorgen dat defecten nooit ontstaan.
Een manier waarop Lean Six Sigma beoefenaars dit kunnen bereiken is door gebruik te maken van failure mode and effects analysis (FMEA), een hulpmiddel voor het identificeren van potentiële problemen en hun impact.
FMEA: The Basics
FMEA is een kwalitatief en systematisch hulpmiddel, meestal gemaakt binnen een spreadsheet, om beoefenaars te helpen anticiperen op wat er mis zou kunnen gaan met een product of proces. Naast het identificeren van hoe een product of proces zou kunnen falen en de effecten van dat falen, helpt FMEA ook bij het vinden van de mogelijke oorzaken van storingen en de kans dat storingen worden ontdekt voordat ze optreden.
Gebruikt in vele industrieën, is FMEA een van de beste manieren om potentiële betrouwbaarheidsproblemen vroeg in de ontwikkelingscyclus te analyseren, waardoor het voor fabrikanten gemakkelijker wordt om snel actie te ondernemen en storingen te beperken. De mogelijkheid om vroegtijdig te anticiperen op problemen stelt ontwerpers in staat om storingen te voorkomen en betrouwbare, veilige en klantvriendelijke functies te ontwerpen.
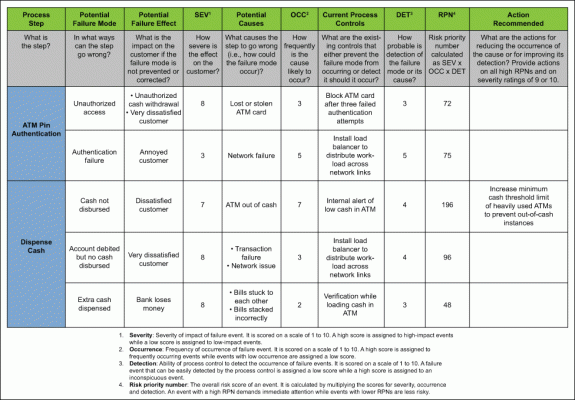
Voorbeeld van FMEA – afbeelding overgenomen uit “Leverage Six Sigma to Manage Operational Risk in Financial Services” (Klik om te vergroten)
Vinden van FMEA Failure Modes
Eén van de eerste stappen bij het invullen van een FMEA is het bepalen van de deelnemers. De juiste mensen met de juiste ervaring, zoals proceseigenaren en ontwerpers, moeten worden betrokken om potentiële faalwijzen te vinden. Professionals zouden ook moeten overwegen om klanten en leveranciers uit te nodigen om alternatieve gezichtspunten te verzamelen.
Als de deelnemers eenmaal bij elkaar zijn, kan het brainstormen beginnen. Bij het invullen van een FMEA is het belangrijk om de Wet van Murphy in gedachten te houden: “Alles wat fout kan gaan, zal ook fout gaan.” De deelnemers moeten alle componenten, systemen, processen en functies identificeren die mogelijk niet aan het vereiste kwaliteits- of betrouwbaarheidsniveau kunnen voldoen. Het team moet niet alleen de effecten van het falen kunnen beschrijven, maar ook de mogelijke oorzaken.
Het voorbeeld in tabel 1 kan worden gebruikt als voorbeeld bij het leren hoe de FMEA werkt. Het team analyseert in dit geval de bandcomponent van een auto.
Tabel 1: FMEA voor autoband
Functie of processtap | Failure Type | Potentiële Impact | SEV | Mogelijke Oorzaken | OCC | Detection Mode | DET | RPN |
Beschrijf wat er fout is gegaan | Wat is de impact op de belangrijkste outputvariabelen of interne vereisten? | Hoe ernstig is het effect voor de klant? | Waardoor gaat de belangrijkste input fout? | Hoe vaak zal dit waarschijnlijk voorkomen? | Wat zijn de bestaande controles die ofwel voorkomen dat de fout optreedt ofwel deze detecteren als hij optreedt? | Hoe gemakkelijk is het op te sporen? | Risicoprioriteit | |
Bandfunctie: gewicht auto ondersteunen, tractie, comfort | Vlakke band | Stopt autorit, bestuurder en passagiers gestrand | 10 | Punctuur | 2 | Bandcontrole vóór rit. Tijdens het rijden trekt het stuur naar één kant, overmatig lawaai | 3 | 60 |
Aanbevolen acties | Verantwoordelijkheid | Target Date | Action Taken | SEV | OCC | DET | RPN |
Wat zijn de acties om het optreden van de oorzaak te verminderen of de opsporing te verbeteren? | Wie is verantwoordelijk voor de aanbevolen actie? | Wat is de streefdatum voor de aanbevolen actie? | Wat zijn de uitgevoerde acties? Bereken nu opnieuw de RPN om te zien of de actie het risico heeft verminderd. | Zorg voor reservewiel en geschikt gereedschap om band te verwisselen | Autobezitter | Vanaf onmiddellijke ingang | Vervangende band en geschikt gereedschap permanent in kofferbak | 4 | 2 | 3 | 24 |
Criteria voor FMEA-analyse
Een FMEA maakt gebruik van drie criteria om een probleem te beoordelen: 1) de ernst van het effect op de klant, 2) hoe vaak het probleem zich waarschijnlijk zal voordoen en 3) hoe gemakkelijk het probleem kan worden opgespoord. De deelnemers moeten een rangorde tussen 1 en 10 (1 = laag, 10 = hoog) vaststellen en overeenkomen voor de ernst, de frequentie en het detectieniveau van elk van de faalwijzen. Hoewel FMEA een kwalitatief proces is, is het belangrijk om gegevens (indien beschikbaar) te gebruiken om de beslissingen die het team neemt met betrekking tot deze beoordelingen te kwalificeren. Een nadere toelichting op de classificaties is te vinden in tabel 2.
Tabel 2: FMEA Ernst, Occurrence en Detection Ratings
Description | Laag getal | Hoog getal | |
Severity | Severity ranking omvat wat belangrijk is voor de industrie, bedrijf of klanten (bijv.g., veiligheidsnormen, milieu, juridisch, productiecontinuïteit, schroot, verlies van zaken, beschadigde reputatie) | Lage impact | Hoge impact |
Rangschikt de waarschijnlijkheid dat een fout zich voordoet tijdens de verwachte levensduur van het product of de dienst | Niet waarschijnlijk | Onvermijdelijk | Detectie | Rangschik de waarschijnlijkheid dat het probleem wordt gedetecteerd en aangepakt voordat het zich voordoet | Zeer waarschijnlijk dat het wordt gedetecteerd | Niet waarschijnlijk dat het wordt gedetecteerd |
Na het rangschikken van de ernst, voorkomen en detectieniveaus voor elke foutmodus, kan het team een risicoprioriteitnummer (RPN) berekenen. De formule voor de RPN is:
RPN = ernst x optreden x detectie
In de FMEA in figuur 1, bijvoorbeeld, heeft een lekke band ernstige gevolgen voor de klant die de auto bestuurt (waardering van 10), maar komt slechts in geringe mate voor (2) en kan vrij gemakkelijk worden gedetecteerd (3). Daarom is de RPN voor deze storing 10 x 2 x 3 = 60.
FMEA-prioriteiten bepalen
Als alle storingen zijn beoordeeld, moet het team de FMEA zodanig aanpassen dat de storingen in aflopende RPN-volgorde worden gerangschikt. Dit geeft aan op welke gebieden correctieve acties kunnen worden gericht.
Er is geen definitieve RPN-drempel om te bepalen welke gebieden de meeste aandacht moeten krijgen; dit hangt af van vele factoren, waaronder industrienormen, wettelijke of veiligheidseisen, en kwaliteitscontrole. Een beginpunt voor het stellen van prioriteiten is echter het toepassen van de Pareto-regel: doorgaans wordt 80 procent van de problemen veroorzaakt door 20 procent van de potentiële problemen. Als vuistregel kunnen teams hun aandacht in eerste instantie richten op de storingen met de top 20 procent van de hoogste RPN scores.
Making FMEA Corrective Actions
Wanneer de prioriteiten zijn overeengekomen, is een van de laatste stappen van het team het genereren van passende corrigerende maatregelen om het optreden van de faalwijzen te verminderen, of in ieder geval om de detectie ervan te verbeteren. De FMEA leider moet de verantwoordelijkheid voor deze acties toewijzen en streefdata voor de voltooiing ervan vaststellen.
Als de corrigerende maatregelen zijn voltooid, moet het team weer bij elkaar komen om de ernst, de waarschijnlijkheid van optreden en de waarschijnlijkheid van detectie voor de belangrijkste faalwijzen opnieuw te beoordelen en te scoren. Zo kan de effectiviteit van de corrigerende maatregelen worden bepaald. Deze evaluaties kunnen nuttig zijn in het geval dat het team besluit dat het nodig is om nieuwe corrigerende maatregelen te nemen.
De FMEA is een waardevol instrument dat kan worden gebruikt om een aantal voordelen te realiseren, waaronder een verbeterde betrouwbaarheid van producten en diensten, het voorkomen van kostbare late ontwerpwijzigingen, en een verhoogde klanttevredenheid.