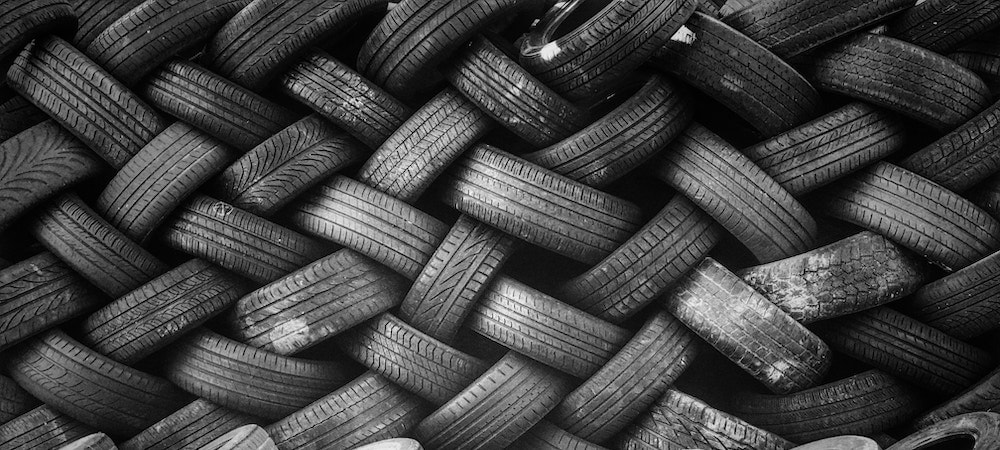

FMEA – failure mode and effects analysis – è uno strumento per identificare potenziali problemi e il loro impatto.
Problemi e difetti sono costosi. I clienti si aspettano comprensibilmente che i produttori e i fornitori di servizi forniscano qualità e affidabilità.
Spesso, i difetti nei prodotti e nei servizi vengono individuati attraverso test approfonditi e modellazione predittiva nelle fasi successive dello sviluppo. Tuttavia, trovare un problema a questo punto del ciclo può aggiungere costi significativi e ritardi ai programmi. La sfida è progettare la qualità e l’affidabilità all’inizio del processo e assicurarsi che i difetti non sorgano mai in primo luogo.
Un modo in cui i professionisti del Lean Six Sigma possono raggiungere questo obiettivo è usare l’analisi delle modalità e degli effetti del fallimento (FMEA), uno strumento per identificare potenziali problemi e il loro impatto.
FMEA: Le basi
FMEA è uno strumento qualitativo e sistematico, solitamente creato in un foglio elettronico, per aiutare i professionisti a prevedere cosa potrebbe andare male in un prodotto o processo. Oltre a identificare come un prodotto o un processo potrebbe fallire e gli effetti di tale fallimento, la FMEA aiuta anche a trovare le possibili cause dei guasti e la probabilità che questi vengano rilevati prima che si verifichino.
Utilizzata in molti settori, la FMEA è uno dei modi migliori per analizzare i potenziali problemi di affidabilità all’inizio del ciclo di sviluppo, rendendo più facile per i produttori agire rapidamente e mitigare il fallimento. La capacità di anticipare i problemi all’inizio permette ai professionisti di progettare senza fallimenti e di progettare caratteristiche affidabili, sicure e piacevoli per il cliente.
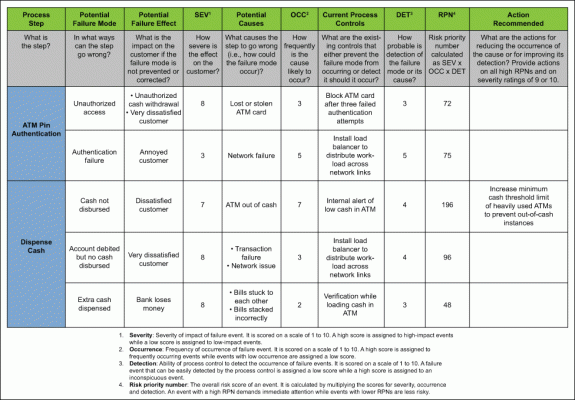
Esempio di FMEA – grafico estratto da “Leverage Six Sigma to Manage Operational Risk in Financial Services” (Clicca per ingrandire)
Finding FMEA Failure Modes
Uno dei primi passi da fare quando si completa una FMEA è determinare i partecipanti. Le persone giuste con la giusta esperienza, come i proprietari del processo e i progettisti, dovrebbero essere coinvolti per catturare potenziali modalità di fallimento. I professionisti dovrebbero anche considerare di invitare clienti e fornitori per raccogliere punti di vista alternativi.
Una volta che i partecipanti sono insieme, il brainstorming può iniziare. Quando si completa una FMEA, è importante ricordare la legge di Murphy: “Tutto ciò che può andare male, andrà male”. I partecipanti devono identificare tutti i componenti, sistemi, processi e funzioni che potrebbero potenzialmente non soddisfare il livello di qualità o affidabilità richiesto. Il team dovrebbe essere in grado non solo di descrivere gli effetti del guasto, ma anche le possibili cause.
L’esempio mostrato nella tabella 1 può essere usato come esempio per imparare come funziona la FMEA. Il team in questo caso sta analizzando il componente del pneumatico di un’automobile.
Tabella 1: FMEA per il pneumatico di un’auto
Funzione o fase del processo | Tipo di guasto | Potenziale Impatto | SEV | Cause potenziali | OCC | Modalità di rilevamento | DET | RPN |
Depilogo della funzione, passo o elemento da analizzare | Descrivere cosa è andato storto | Qual è l’impatto sulle variabili chiave di uscita o sui requisiti interni? | Quanto è grave l’effetto sul cliente? | Cosa causa l’errore dell’input chiave? | Quanto frequentemente è probabile che si verifichi? | Quali sono i controlli esistenti che impediscono che il guasto si verifichi o lo rilevano se si verifica? | Quanto è facile da rilevare? | Numero di priorità del rischio |
Funzione del pneumatico: sostenere il peso dell’auto, trazione, comfort | Pneumatico sgonfio | Arresto del viaggio in auto, conducente e passeggeri bloccati | 10 | Puntura | 2 | Controlli del pneumatico prima del viaggio. Durante la guida, lo sterzo tira da un lato, rumore eccessivo | 3 | 60 |
Azioni consigliate | Responsabilità | Target Date | Azione intrapresa | SEV | OCC | DET | RPN | ||
Quali sono le azioni per ridurre il verificarsi della causa o migliorare il rilevamento? | Chi è responsabile dell’azione raccomandata? | Qual è la data obiettivo per l’azione raccomandata? | Quali sono state le azioni implementate? Ora ricalcolare il RPN per vedere se l’azione ha ridotto il rischio. | ||||||
Trasporto della ruota di scorta e strumenti appropriati per cambiare la gomma | Proprietario dell’auto | Da effetto immediato | Ruota di scorta e strumenti appropriati portati permanentemente nel bagagliaio | 4 | 2 | 3 | 24 |
Criteri per l’analisi FMEA
Una FMEA utilizza tre criteri per valutare un problema: 1) la gravità dell’effetto sul cliente, 2) la frequenza con cui è probabile che il problema si verifichi e 3) la facilità con cui il problema può essere rilevato. I partecipanti devono stabilire e concordare una classifica tra 1 e 10 (1 = basso, 10 = alto) per la gravità, l’occorrenza e il livello di rilevamento per ciascuno dei modi di guasto. Anche se la FMEA è un processo qualitativo, è importante usare i dati (se disponibili) per qualificare le decisioni che il team prende riguardo a queste valutazioni. Un’ulteriore spiegazione delle valutazioni è mostrata nella tabella 2.
Tabella 2: Gravità FMEA, Occurrence and Detection Ratings
Descrizione | Numero basso | Numero alto | |
Severità | La classifica di gravità comprende ciò che è importante per l? azienda o clienti (ad es.g., standard di sicurezza, ambiente, legale, continuità di produzione, scarti, perdita di affari, reputazione danneggiata) | Basso impatto | Alto impatto |
Occurence | Classificare la probabilità che un guasto si verifichi durante la vita prevista del prodotto o servizio | Non è probabile che si verifichi | Inevitabile |
Rilevamento | Classifica la probabilità che il problema venga rilevato e si intervenga prima che sia accaduto | Molto probabile che venga rilevato | Non probabile che venga rilevato |
Dopo aver classificato la gravità, i livelli di occorrenza e di rilevamento per ogni modalità di guasto, il team sarà in grado di calcolare un numero di priorità del rischio (RPN). La formula per l’RPN è:
RPN = gravità x occorrenza x rilevamento
Nella FMEA della figura 1, per esempio, una gomma a terra colpisce gravemente il cliente che guida l’auto (voto 10), ma ha un basso livello di occorrenza (2) e può essere rilevata abbastanza facilmente (3). Pertanto, l’RPN per questa modalità di guasto è 10 x 2 x 3 = 60.
Impostare le priorità della FMEA
Una volta valutate tutte le modalità di guasto, il team dovrebbe modificare la FMEA per elencare i guasti in ordine decrescente RPN. Questo evidenzia le aree in cui le azioni correttive possono essere concentrate. Se le risorse sono limitate, i professionisti devono stabilire prima le priorità sui problemi più grandi.
Non esiste una soglia RPN definitiva per decidere quali aree dovrebbero ricevere la maggiore attenzione; ciò dipende da molti fattori, compresi gli standard industriali, i requisiti legali o di sicurezza e il controllo della qualità. Tuttavia, un punto di partenza per la prioritizzazione è applicare la regola di Pareto: tipicamente, l’80% dei problemi è causato dal 20% dei problemi potenziali. Come regola empirica, i team possono concentrare la loro attenzione inizialmente sui guasti con il 20% dei punteggi RPN più alti.
Fare azioni correttive FMEA
Quando le priorità sono state concordate, uno degli ultimi passi del team è quello di generare azioni correttive appropriate per ridurre l’occorrenza dei modi di guasto, o almeno per migliorare il loro rilevamento. Il leader della FMEA dovrebbe assegnare la responsabilità di queste azioni e stabilire delle date di completamento.
Una volta che le azioni correttive sono state completate, il team dovrebbe riunirsi di nuovo per rivalutare e riclassificare la gravità, la probabilità di accadimento e la probabilità di rilevamento dei principali modi di guasto. Questo permetterà loro di determinare l’efficacia delle azioni correttive intraprese. Queste valutazioni possono essere utili nel caso in cui il team decida che ha bisogno di attuare nuove azioni correttive.
La FMEA è uno strumento prezioso che può essere utilizzato per realizzare una serie di benefici, tra cui una migliore affidabilità di prodotti e servizi, la prevenzione di costose modifiche di progettazione tardive e una maggiore soddisfazione del cliente.