Sabemos que los productos fabricados nunca pueden coincidir perfectamente con sus dibujos teóricos. El tamaño real varía del diseño previsto. El objetivo de GD&T es mantener esta variación dentro de unos límites establecidos.
La posición verdadera es una llamada GD&T para especificar la posición de una característica. Es más correcto referirse a ella como «posición». Utilizamos este concepto en GD&T para controlar la variación de una característica específica desde su posición deseada. Esto es importante para que las piezas que se acoplan garanticen un ensamblaje sin fisuras.
Por ejemplo, los agujeros de los tornillos de una tapa de culata deben coincidir con los agujeros de los tornillos de la carcasa del motor tanto en tamaño como en posición. En caso de que no lo hagan, las dos partes no se acoplarán, y el aceite de lubricación para el conjunto de válvulas se escapará, anulando el propósito de la tapa. La tapa del cilindro es inútil, y hay que utilizar una pieza diferente.
Para evitar que esto ocurra, utilizamos las tolerancias de posición como guía para los servicios de torneado y fresado CNC.
El símbolo de posición es uno extremadamente útil, pero su aplicación puede ser un poco complicada. En este artículo, aprenderemos los fundamentos de esta llamada de característica y cómo aplicar esta herramienta a diferentes condiciones de material.
Definición de posición verdadera
La tolerancia de posición verdadera en GD&T nos informa de la desviación máxima permitida de una característica (por ejemplo, agujero, ranura) de su posición verdadera. Por posición verdadera, nos referimos a la posición ideal de la característica según el diseño.
La idea es que, para una característica, hay una posición verdadera que deseamos. Definimos planos y ejes de referencia para definir la colocación exacta.
A continuación, marcamos las verdaderas posiciones de las características de tamaño utilizando dimensiones básicas. Tenemos en cuenta cualquier modificador de condición de material si es necesario.
La posición es una tolerancia 2D/3D en GD&T que define zonas de tolerancia dependiendo de la característica. Para las características cilíndricas, crea una zona de tolerancia cilíndrica alrededor de la posición verdadera de la característica dentro de la cual debe estar el eje de la característica para todos los productos fabricados.
Para otras características, se definen planos paralelos dentro de los cuales debe estar el plano central de la característica para su aprobación.
Diferencia entre posición y posición verdadera
En la norma ASME Y14.5, la llamada posición verdadera se denomina simplemente «posición». «Posición» es la forma correcta de denominarla, ya que sabemos que la posición verdadera se refiere en realidad al punto teórico en la superficie con dimensiones básicas que es imposible de replicar en los productos reales.
Sin embargo, en la jerga del mecanizado CNC, el término posición verdadera es más popular cuando se refiere a la posición de la característica en el producto real.
Por lo tanto, cuando utilizamos el término ‘posición verdadera’ en el artículo, la mayoría de las veces, nos referimos realmente a la posición de la característica fabricada en relación con la posición verdadera real y no a la posición verdadera (dimensión exacta o valor nominal) de la característica.
-
Cotización en segundos
-
Cortos plazos de entrega
-
Entrega por Fractory
Obtener presupuesto
Tolerancia de posición real vs. Tolerancia lineal
El uso de la tolerancia posicional permite realmente a los diseñadores utilizar tolerancias más holgadas. Hay muchas ventajas en el uso de tolerancias más laxas y es por eso que se hace imperativo que las usemos siempre que sea posible. Veamos cómo el uso de GD&T lo hace posible evaluando dos escenarios con especificaciones de tolerancia similares.
Posición verdadera
Considere un agujero definido con una tolerancia posicional de 1 mm. Esto define una zona de tolerancia circular del radio 0,5 mm alrededor de la posición verdadera. El eje de la característica fabricada debe estar dentro de este círculo de ⌀1 mm, lo que significa que la distancia máxima desde el punto del eje previsto es la misma en todas las direcciones.
Ahora, considere un punto dentro de esta zona de tolerancia a una distancia de 0,25 mm desde el eje X y 0,25 mm desde el eje Y (considerando la posición verdadera como origen).
En este punto, la posición de la característica se calcula como ~0,7 mm, ya que posición = 2 x √(x2 + y2). Este número se encuentra dentro de 1 mm, y por lo tanto, el producto final está dentro del rango aceptable.
Si queremos que esta posición sea el límite superior, tendremos que definir la tolerancia posicional como ⌀0,7 mm.
Tolerancia más/menos
Ahora, vamos a comparar esto con la tolerancia más/menos.
El tolerado más/menos se refiere al método tradicional de asignar tolerancias a las dimensiones de las características. Debido a los límites superior e inferior asignados en cada dirección, la zona de tolerancia resultante es un cuadrado.
Para aceptar el producto fabricado arriba, tendríamos que establecer un límite de tolerancia de ±0,35 mm (Ancho total de tolerancia = 0,7 mm). Esto definiría un cuadrado de lado 0,7 mm.
Al mismo tiempo, las esquinas del cuadrado están más lejos que los lados. Esto significa que la tolerancia dada mediante los ejes X e Y no es uniforme en todas las direcciones.
Comparación
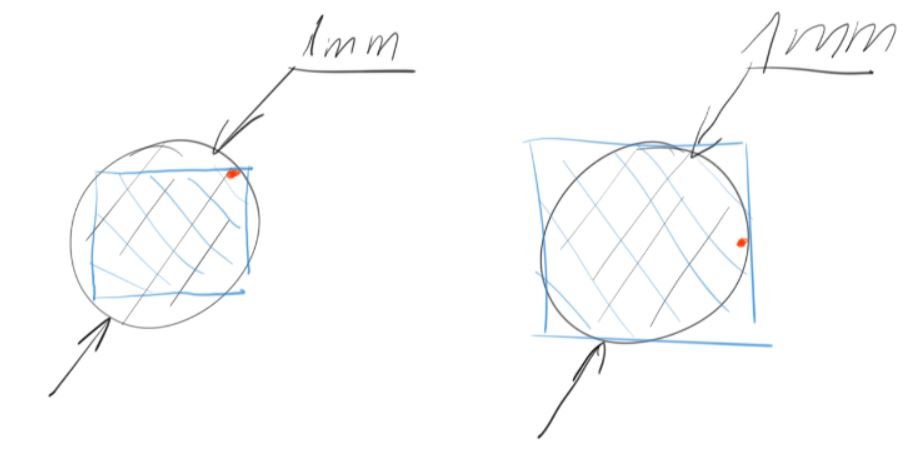
Para que un mismo punto se encuentre en ambas zonas de tolerancia, la zona de tolerancia circular circunscribirá a la zona de tolerancia cuadrada. Si comparamos el área de dos zonas, el área de la zona circular supera a la zona cuadrada.
Podemos calcular la zona extra dividiendo el área del círculo circunscrito por el área del cuadrado. En todos los casos, obtenemos un aumento del 57% en la zona cuando preferimos la tolerancia posicional sobre la tolerancia más/menos.
Así, para la misma desviación, podemos utilizar una tolerancia global más floja y seguir aceptando la pieza. Esto reduce el coste de fabricación de la pieza.
Esto puede ser un poco difícil de comprender. Debemos hacernos la pregunta: ¿Por qué una pieza es aceptable cuando el eje de la característica fabricada está a una distancia de 0,7 mm en las esquinas de un cuadrado pero no es aceptable en los 360 grados?
Utilizar la posición verdadera nos ayuda a explotar el área extra del 57% manteniendo esencialmente el mismo límite.
Características de la zona de tolerancia
La zona de tolerancia utilizando la posición verdadera puede aparecer de dos maneras dependiendo de la llamada utilizada – cilíndrica y cuadrada.
Zona de tolerancia cilíndrica
El símbolo de posición verdadera en GD&T se representa utilizando un símbolo de cruz (⌖). Cuando utilizamos la llamada con un símbolo de diámetro (⌀), obtenemos una zona de tolerancia cilíndrica y así es como se pretende utilizar la mayoría de las veces.
Normalmente, establecemos un punto de referencia para fijar la posición verdadera según nuestro diseño. A veces, podemos utilizar múltiples puntos de referencia para localizar con precisión la característica. Denotamos este punto de referencia utilizando dimensiones básicas.
Esta posición verdadera actúa como nuestra referencia para medir la desviación de las piezas fabricadas reales. La posición verdadera suele fijarse en el centro de la característica que se está tolerando. Por ejemplo, para un agujero, la posición verdadera se establece en el eje del agujero. Alrededor de ella, definimos la zona de tolerancia de diámetro 2D o 3D basada en las características de la característica.
Así, tenemos un eje de referencia para el agujero en la posición verdadera y la zona de tolerancia establece el límite hasta el que el eje de la característica de la pieza real puede desviarse.
La zona de tolerancia 3D es básicamente un cilindro virtual fijado alrededor del eje del agujero en el valor de la tolerancia y pasa por todo el espesor de la pieza.
Zona de tolerancia cuadrada
Sin utilizar el signo de diámetro, la tolerancia de posición real se refiere exactamente a la misma zona cuadrada como lo hace el tolerado lineal tradicional.
Esto crea una zona de tolerancia más ajustada como se ha explicado anteriormente y por ello se utiliza raramente. Podemos perder más del 36% de la zona de tolerancia utilizando la llamada de esta manera.
Cómo utilizar la posición verdadera
La posición verdadera es una de las llamadas más utilizadas en GD&T. Podemos controlar fácilmente la ubicación de diferentes características mediante su uso. Proporciona un método estandarizado para expresar la ubicación disipando cualquier confusión.
Para entender cómo aplicar la posición verdadera a una característica, necesitamos conocer el marco de control de la característica.
Brevemente, el marco de control de la característica consiste en tres bloques principales.
- Símbolo de característica geométrica
- Valor de tolerancia y cualquier modificador de condición de material
- Planos de datos o ejes
Supongamos que necesitamos mostrar, en nuestro dibujo, la posición verdadera y la tolerancia posicional de un agujero situado en el centro de una pieza que mide 100 x 100 x 50 mm(l x b x h). El tamaño del agujero es de ⌀1 mm con una tolerancia de ±0,005 mm.
Selección del tipo de característica geométrica
Como estamos denotando la posición verdadera en el marco de control de la característica, la denotaremos utilizando su símbolo asignado de la cruz (⌖) en el bloque de símbolos de la característica geométrica.
Selección de puntos de referencia
Comenzamos con la selección de nuestro plano de referencia. Podemos utilizar un mínimo de un datum. Los datums pueden ser puntos, líneas o planos.
En este ejemplo de muestra, seleccionaremos tres planos datum. Los nombramos en orden decreciente de importancia.
Para nuestro primer punto de referencia, seleccionaremos el plano inferior de la pieza. Lo llamaremos A. Este dato especifica que el eje del agujero debe ser perpendicular a este plano. Esta es una forma de control de perpendicularidad.
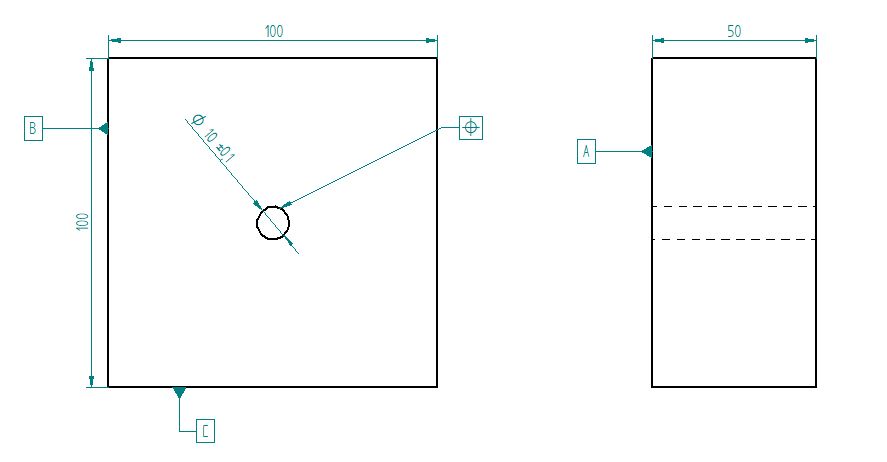
Para nuestros 2º y 3º puntos de referencia, seleccionaremos los planos de la cara izquierda y frontal. Marcaremos estos puntos de referencia como Datum B y C respectivamente en nuestro dibujo de ingeniería.
Entonces, mencionaremos la distancia de nuestra característica (agujero) desde los planos datum B y C en el dibujo. En este caso, es de 50 mm para ambos ya que la posición del agujero está en el centro. Estas distancias se muestran como cotas básicas y se encierran en un recuadro para expresar las mismas.
En el marco de control de la característica, anotaremos A, B y C, en los bloques 3, 4 y 5 respectivamente.
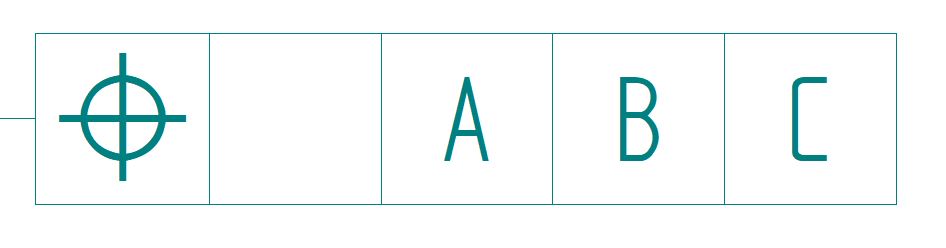
Expresando la zona de tolerancia y los valores
En este ejemplo, utilizaremos la zona de tolerancia cilíndrica. Lo denotaremos en el marco de control de la característica utilizando el símbolo de diámetro (⌀).
Siguiendo esto, denotaremos la anchura total de la tolerancia como 0,01 mm (±0,005 mm).
Modificadores de condición de material
Si hay algún modificador de condición de material presente, lo añadimos después del valor de la tolerancia. Un círculo «M» para la condición máxima del material (MMC), o un círculo «L» para la condición mínima del material (LMC). MMC se utiliza más comúnmente que LMC.
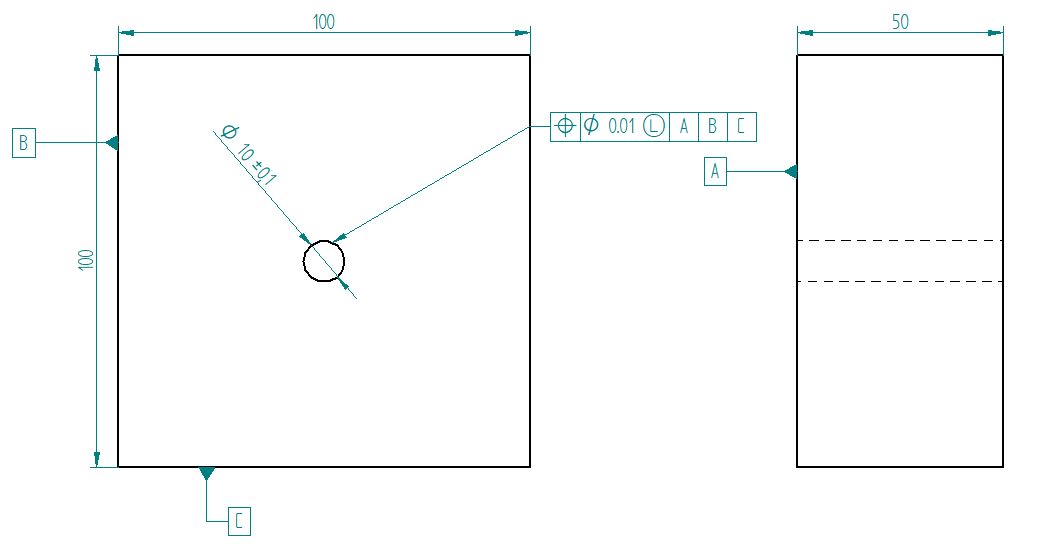
La tolerancia de posición verdadera se utiliza muy a menudo con un modificador de condición de material. Las piezas se toleran en estos límites para asegurar que no interfieren al acoplarse o si lo hacen, ocurre de forma limitada aunque estén en sus límites de tolerancia.
MMC para un eje es el mayor tamaño permitido (diámetro), y para un agujero el menor tamaño permitido. Podemos asegurarnos de que siempre haya alguna holgura entre ambos asegurando que el MMC del eje sea menor que el MMC del agujero en nuestros diseños.
Cuando añadimos este modificador a nuestro marco de control de posición real, especifica que estamos aplicando las tolerancias en la condición de material máximo para asegurar que un agujero no es demasiado pequeño o un eje demasiado grande en cualquier punto a lo largo de la profundidad de la característica. Así, con este tamaño de control de característica, podemos controlar la orientación además del tamaño y la ubicación.
Cómo calcular y medir la posición verdadera
La característica de posición verdadera proporciona muchos usos. Pero cuando se trata de la inspección, es un poco complicado. Empecemos por cómo calcular la posición de una pieza fabricada con respecto a la posición verdadera de la característica.
La posición verdadera se calcula mediante la siguiente fórmula:
Posición verdadera = 2 x Raíz cuadrada, donde
Valor medido – Lectura obtenida por los instrumentos de medición.
Valor real – Posición verdadera declarada mediante cotas básicas.
Estos cálculos se pueden realizar con una simple calculadora o manualmente ya que básicamente es el doble del valor de la hipotenusa obtenido mediante el teorema de Pitágoras.
Si el valor obtenido está dentro del valor de la zona definida, aceptamos la pieza. Hay varias formas de realizar las mediciones de la pieza. Veamos estas opciones.
Máquina de medición por coordenadas (MMC)
Estas máquinas proporcionan una gran precisión a la hora de realizar las mediciones. Normalmente, los talleres mecánicos con máquinas CNC tendrán una máquina de medición de coordenadas que mide las piezas y realiza todos los cálculos de forma digital.
Esta es la forma más precisa de medir la posición real. La máquina contiene una bola en el extremo de un brazo robótico. Guiamos la bola hacia la característica que necesitamos medir. A continuación, traza la característica y convierte el movimiento en el perfil de la característica mediante el software incorporado.
El método de medición puede ser un poco confuso. Por ello, hemos anotado los pasos generales que pueden ser de ayuda. Seguimos los siguientes pasos a la hora de medir con una MMC.
Mide tus puntos de referencia
Comprueba la impresión y localiza tus puntos de referencia. Por ejemplo, digamos que A es una superficie datum. El punto de referencia B es un eje de referencia, y C es un origen de referencia.
Alinear la pieza
Nivelar el plano. Gire a la línea y establezca el origen como el punto de referencia C.
Medir características
Identifique la cota llamando a la posición verdadera y mídala.
Dimensionar posición
Ahora, haga clic en Dimensión y seleccione la posición. A continuación, informe de ella.
En caso de que esté utilizando marcos de control de características, debe definir los puntos de referencia en el editor antes de elegir las características que desea informar.
Calibre especial
Podemos utilizar un conjunto especial de calibradores conocidos como el calibre digital de distancia central para medir la posición. Este calibrador puede medir la distancia central entre dos agujeros o agujeros de paso. Pueden medir una gama de tamaños de centros de agujeros.
Podemos utilizarlo para la medición de pasos así como para la medición externa. Son fáciles de usar con funciones de bloqueo, ajuste fino y preajuste de datos.
Medidor funcional fijo
Es probablemente la forma más rápida de medir la posición real. Generalmente vemos su uso en la fabricación de alto volumen debido a su eficiencia. Un calibrador funcional mide sólo la posición y no el tamaño de la característica.
Por ejemplo, para una pieza de trabajo con un agujero, el calibrador sería un bloque con un pasador que sobresale en la posición verdadera del agujero y otras características para alinear a los puntos de referencia. Si el pasador puede entrar en el agujero cuando el calibre está alineado con el punto de referencia, aceptamos la pieza. El tamaño de la característica tiene que ser medido por separado.