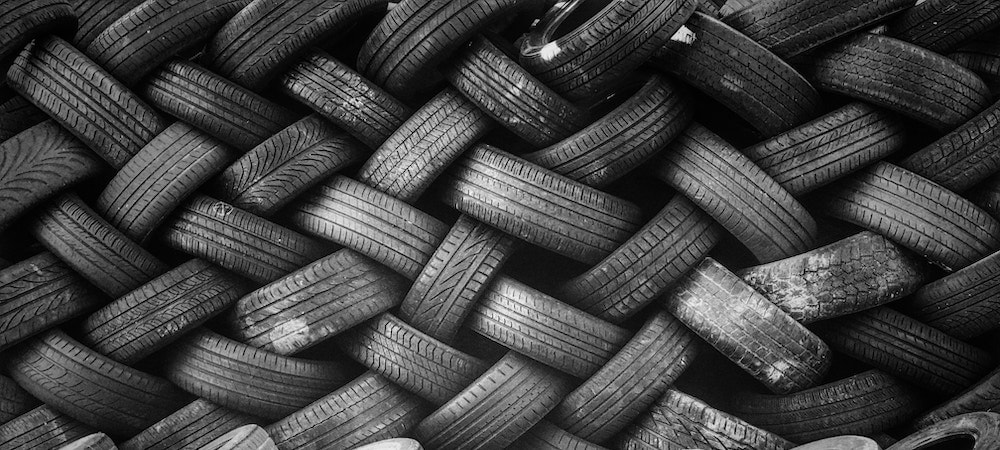

FMEA -análisis de modos de fallo y efectos- es una herramienta para identificar problemas potenciales y su impacto.
Los problemas y los defectos son caros. Los clientes, comprensiblemente, depositan grandes expectativas en los fabricantes y proveedores de servicios para que ofrezcan calidad y fiabilidad.
A menudo, los fallos en los productos y servicios se detectan a través de extensas pruebas y modelos predictivos en las últimas fases de desarrollo. Sin embargo, encontrar un problema en este punto del ciclo puede añadir un coste significativo y retrasos en los calendarios. El reto consiste en diseñar la calidad y la fiabilidad al principio del proceso y garantizar que los defectos nunca surjan en primer lugar.
Una forma en la que los profesionales de Lean Six Sigma pueden lograr esto es utilizar el análisis del modo de fallo y los efectos (FMEA), una herramienta para identificar los problemas potenciales y su impacto.
FMEA: lo básico
FMEA es una herramienta cualitativa y sistemática, normalmente creada dentro de una hoja de cálculo, para ayudar a los profesionales a anticipar lo que podría ir mal en un producto o proceso. Además de identificar cómo podría fallar un producto o proceso y los efectos de ese fallo, el FMEA también ayuda a encontrar las posibles causas de los fallos y la probabilidad de que se detecten antes de que se produzcan.
Utilizado en muchos sectores, el FMEA es una de las mejores formas de analizar los posibles problemas de fiabilidad en una fase temprana del ciclo de desarrollo, lo que facilita que los fabricantes tomen medidas rápidas y mitiguen los fallos. La capacidad de anticiparse a los problemas con antelación permite a los profesionales diseñar los fallos y las características fiables, seguras y agradables para el cliente.
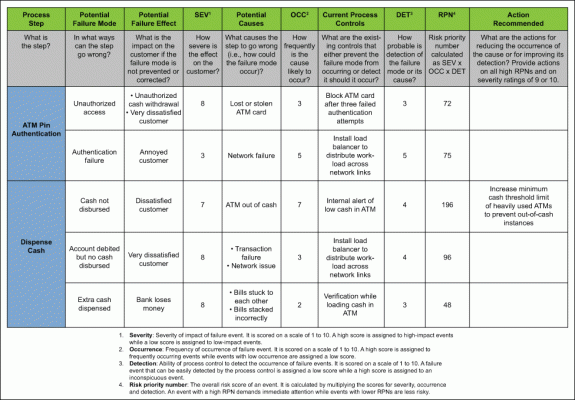
Ejemplo de FMEA – gráfico extraído de «Leverage Six Sigma to Manage Operational Risk in Financial Services» (Haga clic para ampliar)
Encontrar los modos de fallo del FMEA
Uno de los primeros pasos que hay que dar al completar un FMEA es determinar los participantes. Deben participar las personas adecuadas con la experiencia adecuada, como los propietarios de los procesos y los diseñadores, con el fin de detectar posibles modos de fallo. Los profesionales también deberían considerar la posibilidad de invitar a clientes y proveedores para reunir puntos de vista alternativos.
Una vez reunidos los participantes, puede comenzar la lluvia de ideas. Al completar un AMFE, es importante recordar la Ley de Murphy: «Todo lo que puede salir mal, saldrá mal». Los participantes deben identificar todos los componentes, sistemas, procesos y funciones que potencialmente podrían fallar para alcanzar el nivel de calidad o fiabilidad requerido. El equipo no sólo debe ser capaz de describir los efectos del fallo, sino también las posibles causas.
El ejemplo que se muestra en la Tabla 1 puede utilizarse como ejemplo a la hora de aprender cómo funciona el AMFE. El equipo en este caso está analizando el componente del neumático de un coche.
Tabla 1: FMEA para un neumático de coche
Función o paso del proceso | Tipo de fallo | Potencial Impacto | SEV | Causas Potenciales | OCC | Modo de Detección | DET | RPN | Resuma brevemente la función paso o elemento que se está analizando | Describa qué ha fallado | ¿Cuál es el impacto en las variables de salida clave o en los requisitos internos? | ¿Cuál es la gravedad del efecto para el cliente? | ¿Qué hace que el insumo clave salga mal? | ¿Con qué frecuencia es probable que ocurra? | ¿Cuáles son los controles existentes que impiden que se produzca el fallo o lo detectan en caso de que ocurra? | ¿Qué tan fácil es detectarlo? | Número de prioridad del riesgo |
Función de los neumáticos: soportan el peso del coche, tracción, confort | Se pinchan | Se detiene el viaje del coche, conductor y pasajeros se quedan tirados | 10 | Pinchazos | 2 | Revisiones de los neumáticos antes del viaje. Durante la conducción, la dirección tira hacia un lado, exceso de ruido | 3 | 60 |
Acciones recomendadas | Responsabilidad | Fecha objetivo | Acción tomada | SEV | OCC | DET | RPN |
¿Cuáles son las acciones para reducir la ocurrencia de la causa o mejorar la detección? | ¿Quién es el responsable de la acción recomendada? | ¿Cuál es la fecha objetivo para la acción recomendada? | ¿Cuáles fueron las acciones implementadas? Ahora vuelva a calcular el RPN para ver si la acción ha reducido el riesgo. | ||||
Propietario del coche | De inmediato | 4 | 2 | 3 | 24 | ||
Criterios para el análisis FMEA
Un FMEA utiliza tres criterios para evaluar un problema: 1) la gravedad del efecto sobre el cliente, 2) la frecuencia con la que es probable que se produzca el problema y 3) la facilidad con la que se puede detectar el problema. Los participantes deben establecer y acordar una clasificación entre 1 y 10 (1 = bajo, 10 = alto) para la gravedad, la frecuencia y el nivel de detección de cada uno de los modos de fallo. Aunque el AMFE es un proceso cualitativo, es importante utilizar datos (si están disponibles) para calificar las decisiones que el equipo toma en relación con estas clasificaciones. Una explicación más detallada de las calificaciones se muestra en la Tabla 2.
Tabla 2: Gravedad del AMFE, Calificaciones de ocurrencia y detección
Descripción | Número bajo | Número alto | Severidad | La clasificación de la gravedad abarca lo que es importante para la la empresa o los clientes (p. ej.g., normas de seguridad, medio ambiente, legal, continuidad de la producción, chatarra, pérdida de negocio, reputación dañada) | Impacto bajo | Impacto alto |
Ocurrencia | Califica la probabilidad de que se produzca un fallo durante la vida útil prevista del producto o servicio | No es probable que ocurra | Inevitable |
Detección | Clasifica la probabilidad de que el problema sea detectado y se actúe sobre él antes de que se haya producido | Muy probable que se detecte | Poco probable que se detecte |
Después de clasificar la gravedad, ocurrencia y niveles de detección para cada modo de fallo, el equipo podrá calcular un número de prioridad de riesgo (RPN). La fórmula para el RPN es:
RPN = gravedad x ocurrencia x detección
En el FMEA de la Figura 1, por ejemplo, un neumático pinchado afecta gravemente al cliente que conduce el coche (calificación de 10), pero tiene un bajo nivel de ocurrencia (2) y puede detectarse con bastante facilidad (3). Por lo tanto, el RPN para este modo de fallo es 10 x 2 x 3 = 60.
Establecer las prioridades del AMFE
Una vez evaluados todos los modos de fallo, el equipo debe ajustar el AMFE para enumerar los fallos en orden descendente de RPN. Esto resalta las áreas en las que se pueden enfocar las acciones correctivas. Si los recursos son limitados, los profesionales deben establecer prioridades en los problemas más grandes primero.
No hay un umbral RPN definitivo para decidir qué áreas deben recibir la mayor atención; esto depende de muchos factores, incluyendo las normas de la industria, los requisitos legales o de seguridad y el control de calidad. Sin embargo, un punto de partida para la priorización es aplicar la regla de Pareto: normalmente, el 80% de los problemas son causados por el 20% de los problemas potenciales. Como regla general, los equipos pueden centrar su atención inicialmente en los fallos con el 20 por ciento de las puntuaciones RPN más altas.
Realización de las acciones correctivas del AMFE
Una vez acordadas las prioridades, uno de los últimos pasos del equipo es generar las acciones correctivas adecuadas para reducir la aparición de los modos de fallo o, al menos, para mejorar su detección. El líder del AMFE debe asignar la responsabilidad de estas acciones y establecer las fechas de finalización.
Una vez que se hayan completado las acciones correctivas, el equipo debe reunirse de nuevo para reevaluar y volver a puntuar la gravedad, la probabilidad de ocurrencia y la probabilidad de detección de los modos de fallo más importantes. Esto les permitirá determinar la eficacia de las medidas correctoras adoptadas. Estas evaluaciones pueden ser útiles en caso de que el equipo decida que necesita promulgar nuevas acciones correctivas.
El AMFE es una herramienta valiosa que puede utilizarse para obtener una serie de beneficios, como la mejora de la fiabilidad de los productos y servicios, la prevención de costosos cambios de diseño tardíos y el aumento de la satisfacción del cliente.